What Makes Drop Forging Best for Industrial Metal Components?
Drop, press, rolling, hot, cold, warm; there is a wide variety of processes that forging materials can take to manufacture parts for today’s consumers and enterprises. However, there is one manufacturing process that stands out among them all for value, time, and dependability: drop forging.
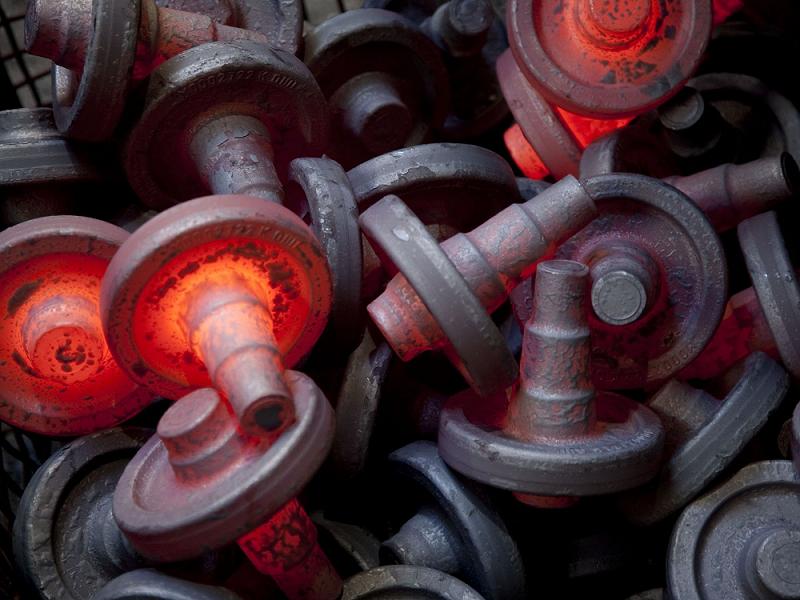
Similar to press, and ring rolled forgings, with closed-die drop forgings the billet is heated to a point of most malleability without changing to liquid state; it remains in a solid state the entire forging process. Casting on the other hand takes a material and heats it completely to the melting point and pours this liquid metal into a formed cast (see casting vs forging). This is easier to produce more geometrically complex shapes however, the durability and overall quality is lesser, takes more resources, and is not as cost effective with material scrap. Drop forgings minimize wasted material and are cost-effective, quick, and retain their durability under considerable stresses. This makes drop forging best for industrial metal components.
The applications of drop forgings are as versatile as an industry needs them to be. From the smallest 0.5 pounds forging to massive parts weighing 100 pounds, carbon steel, stainless steel, and alloy steel forgings can be found anywhere. Automotive, Aerospace, Mining, and Off-Highway are just a few examples of industries that have demand of drop forgings. These industries have determined over time that drop forgings are the best option for cost-effectiveness, durability, and on-demand production.
With plenty of other uses for drop forgings in many industries, Fly Forge is happy to supply the highest of quality forgings to anyone who seeks them. You will be pleased to cooperate with such a reliable supplier as our drop forgings really can impact your business and win more orders from your customer.
Related Article: Where Can I Get High Quality Drop Forgings?
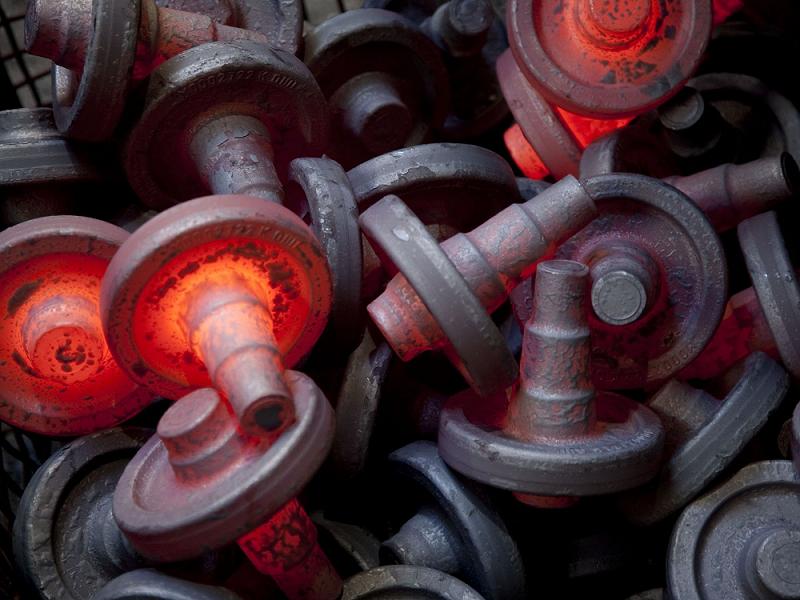
Similar to press, and ring rolled forgings, with closed-die drop forgings the billet is heated to a point of most malleability without changing to liquid state; it remains in a solid state the entire forging process. Casting on the other hand takes a material and heats it completely to the melting point and pours this liquid metal into a formed cast (see casting vs forging). This is easier to produce more geometrically complex shapes however, the durability and overall quality is lesser, takes more resources, and is not as cost effective with material scrap. Drop forgings minimize wasted material and are cost-effective, quick, and retain their durability under considerable stresses. This makes drop forging best for industrial metal components.
The applications of drop forgings are as versatile as an industry needs them to be. From the smallest 0.5 pounds forging to massive parts weighing 100 pounds, carbon steel, stainless steel, and alloy steel forgings can be found anywhere. Automotive, Aerospace, Mining, and Off-Highway are just a few examples of industries that have demand of drop forgings. These industries have determined over time that drop forgings are the best option for cost-effectiveness, durability, and on-demand production.
With plenty of other uses for drop forgings in many industries, Fly Forge is happy to supply the highest of quality forgings to anyone who seeks them. You will be pleased to cooperate with such a reliable supplier as our drop forgings really can impact your business and win more orders from your customer.
Related Article: Where Can I Get High Quality Drop Forgings?