
Drop forging manufacturer

Besides the control of aluminum forging temperature, the design of aluminum forging component is also very important. Parts design mainly includes the standards for machining allowances, parting line location, draft angles, corner and fillet radii for the aluminum forging.
Machining Allowances
Recommended machining allowance for aluminum forging is given in below Table.
Greatest Dimension (mm) | Minimum Finish Stock per Surface (mm) |
Less than 200 | 1.6 |
200 to 400 | 2.4 |
400 to 600 | 3.2 |
600 to 900 | 4 |
More than 900 | 4.8 |
As shown above, the allowance is referred to as minimum finish stock per surface and is related to the largest dimension of forging. Machining allowance may be applied over the entire forging or to the surfaces to be machined. The finish allowance is applicable to all metals.
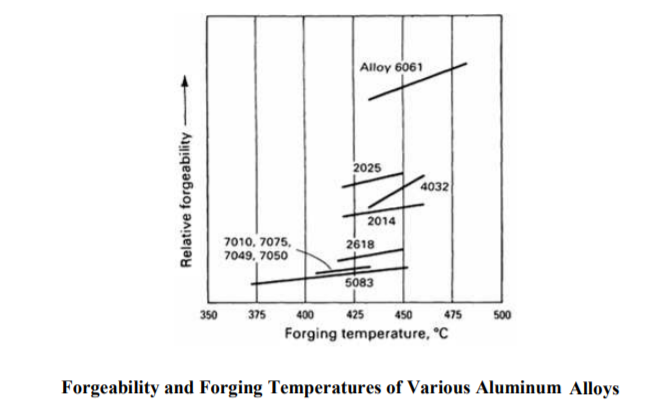
On the other hand, with the temperature increase of aluminum billets after heating, the forgeability of all aluminum alloys will also be improved. As the forgeability of each aluminum alloy is different, the heating temperature required during hot forging process is also different. Below picture shows forgeability of different aluminum alloys with respect to temperature changes are given. From this picture we can well see that as the temperature increases forgeability increases.
As you know, forging is better for applications. 6061 and 7075 are the two common used alloys in aluminum forging. When it comes to 6061 aluminum alloy or 7075 aluminum alloy for a forging project, it is necessary to understand their differences and applications. It saves you trouble when looking to balance performance with cost. For most general purposes, both alloys can get the job done. But the differences in composition, mechanical properties and cost can help you choose what fits your forging needs best.
The chemical differences between 6061 and 7075 aluminum forgings aren’t readily visible. Both contain magnesium, silicon, copper, iron, zinc, titanium, manganese and chromium. The difference is how much of each is contained in each. 6061 aluminum forging contains less zinc than 7075. Meaning that while 6061 aluminum forging provide superior welding abilities and workability, it doesn’t boast the same high strength and stress resistance as 7075. Looking for a good aluminum forging company in China for your item? Pls contact CFS Forge!
The chemical differences between 6061 and 7075 aluminum forgings aren’t readily visible. Both contain magnesium, silicon, copper, iron, zinc, titanium, manganese and chromium. The difference is how much of each is contained in each. 6061 aluminum forging contains less zinc than 7075. Meaning that while 6061 aluminum forging provide superior welding abilities and workability, it doesn’t boast the same high strength and stress resistance as 7075. Looking for a good aluminum forging company in China for your item? Pls contact CFS Forge!
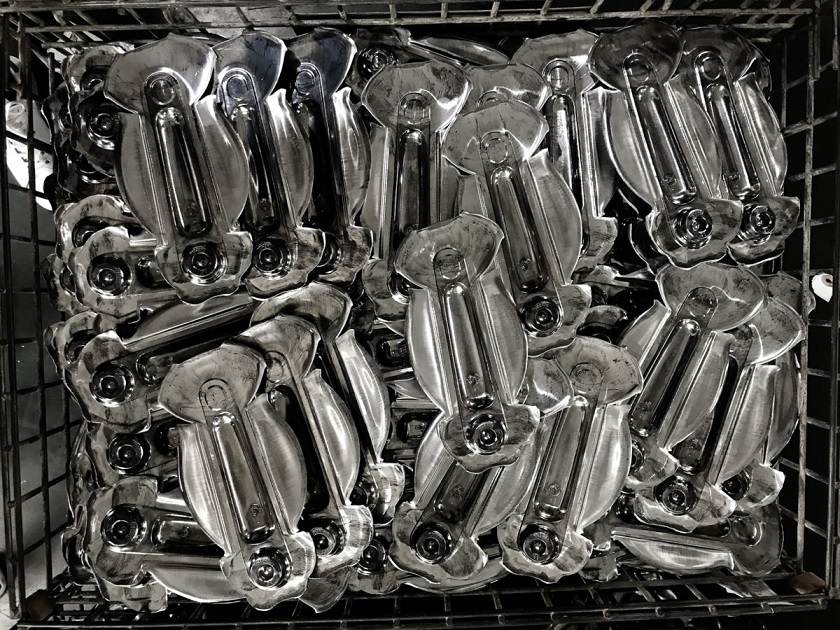
After a new aluminum forged product is designed, a lot of companies would be ready to make the design into production from China for its low production cost. At this point, it will be of great importance to select a proper aluminum forging manufacturer. Personally, I’ve been working in the aluminum forging industry for many years, and have known lots of aluminum forging manufacturers, big or small. In this article, I am going to sum up my years of understanding and experience in the profession and would be happy to share it with all of you.
When you search “China aluminum forging manufacturer “or” Chinese aluminum forging company” in Google, you will get a lot of contacts from aluminum forging manufacturers in China, I suggest you send RFQs to 2 or more aluminum forging companies, then you can compare their prices, they react speed, their professional support. Normally the aluminum forging manufacturer arranges an engineer or a sales who have the engineering background to contact you, it will be much better than a sales girl without any engineering experience. Because aluminum forging is a customize and professional service, aluminum forging experience will help a lot in communication and avoid misunderstanding in engineering. it will save lots of time and cost. When you decide to work with one aluminum forging manufacturer, I suggest to visit them on site, then you can check their facility and talk to them face to face. if time or budget is limited, then you can ask for some reference customers from your own country who are dealing with them, the people who live in the same country and culture are always more trustworthy.
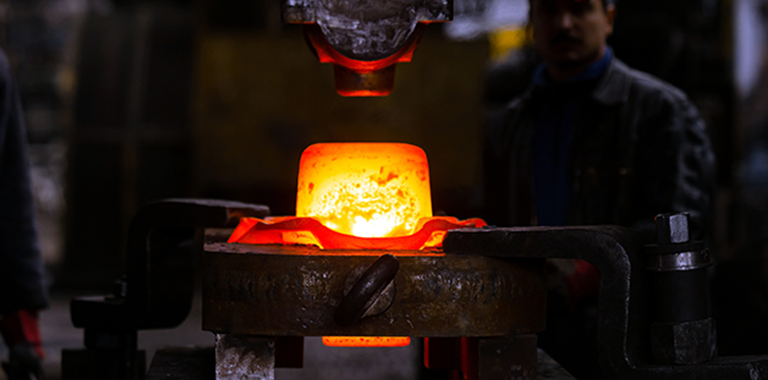
As the name suggests, the process of hot forging requires the heating of the metal, so the heating temperature has a significant impact on the forming process and result. In order to ensure the forgability of the metal and obtain good internal structure performance, the forging heating must follow certain heating specifications and carry out the forging process within the specified temperature. At the same time, because the temperature of the blank metal is very high, sometimes the mold also needs preheating, so there are certain requirements for the life of the mold and forming equipment. In order to ensure the progress of the forging process, the following major issues need to be considered during hot forging process:
In hot forging, the metal blank is heated to a certain temperature before forging. Can reduce the strength of the metal limit b sigma, improve its plasticity, and the higher the heating temperature, the greater the b sigma reduction, the required forming force is lower. In order to reduce the forming force and energy consumption, the heating temperature of the metal blank should be raised as far as possible on the premise of avoiding the occurrence of overburning of the metal. As the aluminum forging temperature range is narrow, so we should pay more attention to the control of pre-forging heating.
In the process of forging, not only the appropriate shape and size must be required, but also the performance requirements of the parts during the use must be met, which includes strength index, plasticity index, impact toughness, fatigue strength, fracture toughness, resistance against stress corrosion and so on. This makes forging process always better than other metal working processes.
compared with other processes (casting or machining), forging is always better. CFS Forge is the professional drop forging company, we can deal with drop forging process with different materials: steel, aluminum and copper. Contact us if you have any forging source from China.
compared with other processes (casting or machining), forging is always better. CFS Forge is the professional drop forging company, we can deal with drop forging process with different materials: steel, aluminum and copper. Contact us if you have any forging source from China.
People usually see the words "drop forged" stamped on so many tools. You may wonder what the big deal is! Why do manufacturers want you to know that a tool is drop forged?
If you have ever seen a blacksmith beating on a piece of red hot iron with a hammer, you have seen the simplest type of forging. Striking a piece of hot metal with a hammer is forging, and blacksmiths have been doing this for centuries. As blacksmiths experimented with new techniques, they learned that complex shapes could be created by hammering metal into a die. The die contains the shape of the finished product. Modern manufacturers use either a falling hammer or a powered hammer to do the hammering (rather than doing it by hand), and usually use dies on both sides of the piece. This is drop forging.
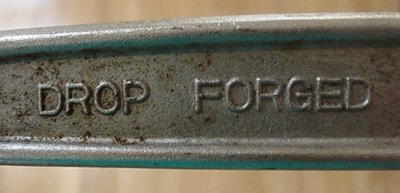
Aluminum cold forging utilizes the plasticity of aluminum alloys at room temperature to shape them. Before this processing method was applied, metals were mainly finished by cutting. But cutting materials down from the start is time consuming and produces a large amount of shavings. That is why so much interest is being shown in cold forging, because this technique makes processing times shorter and does not produce shavings.
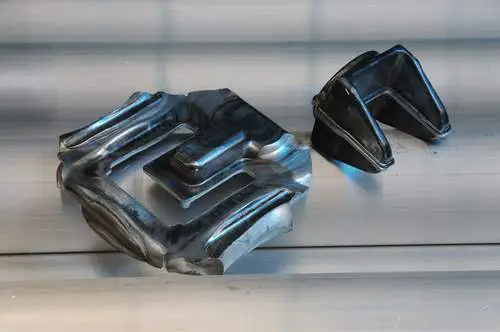
To save costs, lots of foreign buyers are happy to make aluminum forgings in China. We all know that a reliable supplier can not only help to supply good quality products, but also save costs for you. Then, how to choose a good aluminum forging supplier in China? Before you place your first order to a new aluminum forging supplier in China, you need to be very careful for the choice you make, which Chinese manufacturer you should go? There are terrible stories, consequence of wrong choices made, that I heard more than once from my friends from west. As a local Chinese aluminum forging company, I would like to share some guidelines with you.
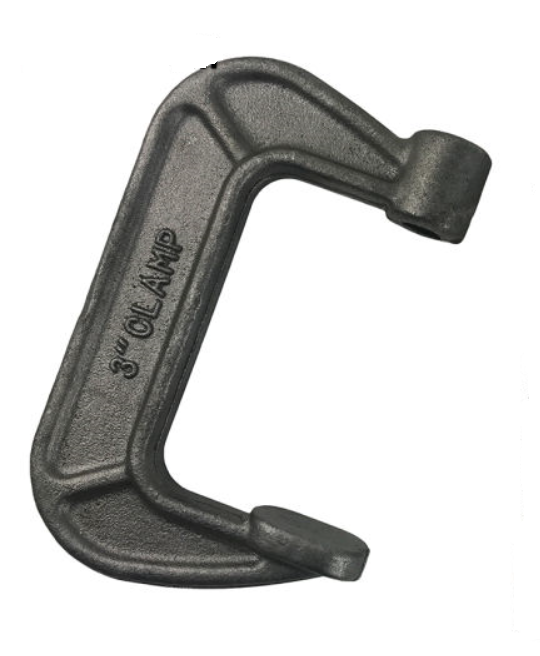
CFS Forge is the premier forged steel c clamps provider. Operating out of six production lines in china, one of our greatest strengths is in the diversity of solutions we offer. The types of forged steel c clamps we produce can be in different sizes, ranging from 0.5kg up to 10kgs. Located in Ningbo, China, we have cooperated shipping company to deliver goods to our customers. Together with value added services, allowing us to stay competitive and directly supply finished product to our customers.