
Drop forging manufacturer

Drop forging has long been a popular method for manufacturing metal parts, but it is not the only option. Casting, machining, stamping, and extrusion are all viable alternatives that may be better suited to certain applications. By understanding the benefits of each method, you can choose the process that will best meet their needs.
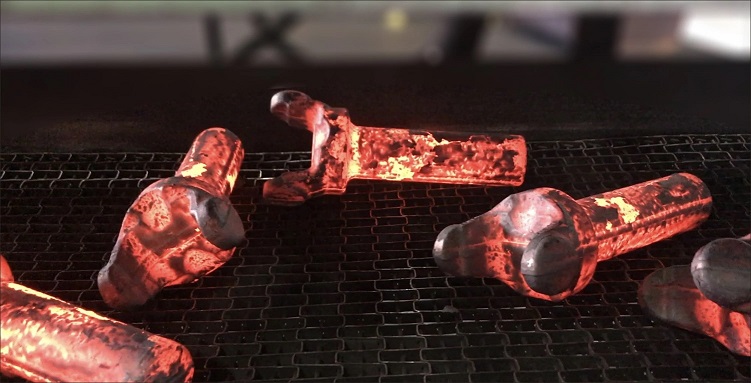
Drop forging is a manufacturing process that involves heating metal to a high temperature and then using a hammer or press to deform the metal into the desired shape. The process is called "drop forging" because the metal is dropped into the forging machine. The metal is typically heated to a temperature of around 2200 degrees Fahrenheit, which makes it more malleable and easier to shape. Once the metal is heated, it is placed in the forging machine, and the hammer or press is used to apply pressure to the metal, shaping it into the desired form.
CFS Forge is the top drop forging company in China, we can provide drop forging services in different materials, including steel, aluminum and brass. If you have a question on the selecting of the material for your drop forged items, pls do not hesitate to contact us. We are pleased to help you based on our rich experience on drop forging technique!
In this article, we will discuss the steps involved in creating custom forged components with drop forging. We will also highlight the benefits of drop forging and provide tips for selecting a reliable drop forging supplier.
Choosing an aluminum forging company from China requires careful consideration of a variety of factors. You should look for a good aluminum forging company like CFS Forge. By evaluating these factors and choosing the right company, you can ensure that your aluminum forging needs are met with high-quality products and excellent service.
In recent years, China has emerged as a leading producer of aluminum forgings, with a growing number of companies specializing in this field. In this article, we will explore the advantages of choosing an aluminum forging company from China and why it is becoming an increasingly popular option for businesses around the world.
Aluminum forging is a versatile and effective manufacturing process used in many industries. By following the steps outlined in this guide and using the tips provided, you can perform successful aluminum forging and create high-quality products that meet your customers' needs. Remember to choose the right aluminum alloy, control the temperature, use the right equipment, and work with an experienced forging company to achieve the best results. With proper preparation, heating, forging, cooling, and finishing, you can create durable and corrosion-resistant aluminum products that meet the highest standards of quality and performance.
In summary, aluminum forging is a complex process that requires careful preparation, monitoring, and control to achieve the desired results. CFS Forge is a professional aluminum forging company, we can produce forged aluminum parts to any specification required. If you need any aluminum forging service, pls remember to contact our forging company!
Choosing the right aluminum alloy for forging is critical to achieving the desired properties and performance of the finished product. Each of the aluminum forging alloys listed above has its unique properties and characteristics, and selecting the right one depends on several factors. By considering these factors, you can select the right aluminum alloy for your specific application and ensure the quality and durability of your forged aluminum part.
The surface finish of aluminum forgings plays a critical role in determining the quality, appearance, and durability of the final product. Achieving a smooth and even surface finish requires careful consideration of several factors. There are several ways can be used to improve the surface finish of aluminum forgings. By understanding the importance of surface finish and selecting the appropriate technique, we can produce high-quality aluminum forgings that meet the desired specifications and requirements of our customers.
No matter what kind of surface finish is required for aluminum forgings, CFS Forge can always meet your demands. If you are looking for a reliable aluminum forging company for your project, pls contact us right now!
Aluminum forging has emerged as a superior material choice for control arms in automotive manufacturing. The use of aluminum forging for control arms has several benefits, including improved performance, increased durability, and reduced weight. In this article, we will explore why aluminum forging is a superior material choice for control arms and how it can benefit automotive manufacturers.
Control arms are an essential component of the suspension system in automobiles. They connect the steering knuckle to the vehicle's frame and help maintain the proper wheel alignment, ensuring that the wheels stay in contact with the road. Control arms are subjected to significant loads and stresses, and they need to be strong, durable, and lightweight to ensure optimal performance and reliability.
CFS Forge is a professional drop forging company in China. We are able to customize either forged aluminum control arms or forged steel control arms. Any inquiry on forged control arms, pls feel free to contact us!
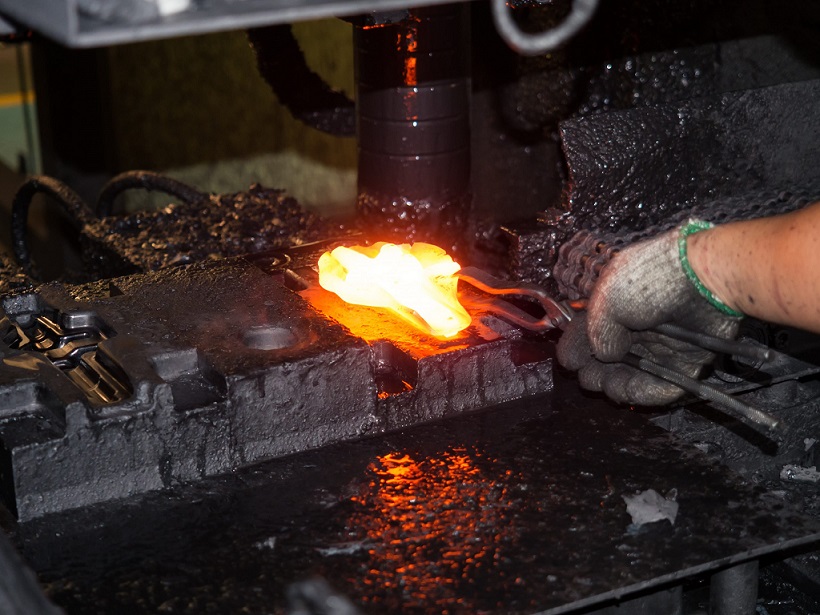
When deciding between drop forging and casting, it's important to consider the specific requirements of your project. If you need parts that are strong, precise, and have a good surface finish, drop forging is likely the better choice. If you need parts with greater design flexibility, faster lead times,and are willing to accept some trade-offs in strength and precision, casting may be the better option.
Another factor to consider is the production volume. Drop forging is generally more cost-effective for larger production runs, while casting may be more cost-effective for smaller runs.
It's also worth noting that there are variations of both drop forging and casting that can be used to further tailor the manufacturing process to your specific needs. For example, there are different types of drop forging, such as open die forging and closed die forging, which can be used to produce different types of parts.