Modern manufacturing process of forged connecting rod
Over the past 50 years,automotive forging manufacturing technology is in the continuous improvement.Today,what takes a leading role in the market is the low cost,high strength anf tight tolerance.In drop forging production process,the strict requirements for forgings are just as important as to the requirements of the finished product.Drop forging companies around the word constantly look for a better production method to achieve the objectives and requirements of the auto parts buyers.
Forged connecting rods are regarded as the quality standards of internal combustion engine to use for decades.Over the years,production methods of connecting rods are constantly changed,includingforging hammer forging,press forging,metal powder forging and casting.In the early years of auto industry development,forging hammer forging is considered to be one of the best forging method.However,in the middle of the twentieth century,due to the higher requirements for quality and tolerance,the forging method must be changed,so manufacturers began to use mechanical press to replace forging hammer.The most effective way to reduce the manufacturing cost is to improve the material utilization.Increasingly stringent requirements for weight and size tolerance promotes the use of powder forging method.Another advantage in addtion to tolerance is that we could forge connecting rod cover toegther with connecting rod,and can open the cover from connecting rod,thus manufacturing cost can be saved.In the late twentieth century, forging method developed into "open" forged steel connecting rods(Why use steel for drop forged connecting rods in automotive cylinder engine?),it is also one of the strengths of the powder forging.The strength of forged steel connecting rod is higher than powder metallurgy rod.Increase as the engine compression ratio,compared with the powder forging connecting rod(wrought vs powder forged connecting rods),high strength of forged steel connecting rod becomes more satisfactory,this forging method can meet the both strict requirements of weight and size tolerance.
This paper mainly describes the modern production technology and die design method,this method is a very successful forging process.According to such forging process of connecting rods,statistical results show that the weight tolerance is less than 4g,thickness tolerance is less than +/-5mm.
Background
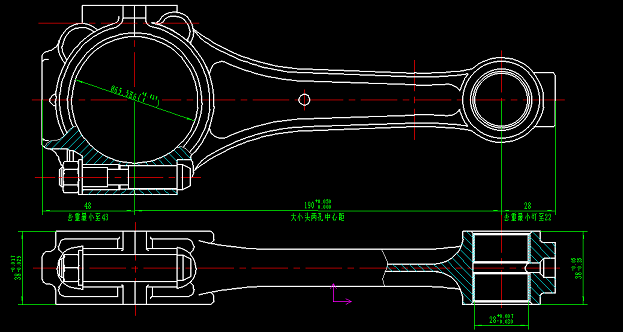
This forging part is a single part weighting 540 grams,the distance from the centerline of the connecting rod to the centerline is 129.6 mm (as shown in the figure below).Weight tolerance requirement of forged connecting rod in the drawing is +/-10g.Total thickness difference allows for +.4/-.2mm. Material of connecting rod is 40 Cr.
Process
Process design starts from using our CADIF (spreadsheet) program on the analysis of the forging process,CADIF program is to use a simplified geometry and material properties at high temperatures to estimate required equipment specifications,the quantities of the die chamber and the production efficiency.Here,we use AISI4140 as product material,and execute the # 14 die forging hammer (14000 ft-lb,19 kJ) analysis.CADIF input part of a display is as follows for your reference
After the assessment of the input,CADIF recommend a # 14 die forging hammer.Forging process will be 5 times preforging and 1 time forming forging.The estimated die life is for 20000pcs forged connecting rods.
Analysis can also estimate other process parameters like trimming tonnage,production efficiency and heating load.The optimal size of the induction heating power rating of 400-500kW.The generated output as shown below
You can now continue to push forward the design of dies,this design starts from forming materials distribution.Forming forging platter as shown in the figure below,like what we see from the picture,forging platter is designed as one module and two chambers,end to end,with the crank end embedded to enhance the platter.To some extent,the generated design depends on the method of forging.In this case,can use roller of cross wedge rolling mill to produce a circular cross section.Complete design of the platter as below model.
This operation is flattened in the forging hammer,in order to better distribute material,to better cover preforging die chamber.Die design using a multi-step straightening machine,such as mold pictures below.Straightening machine will be placed in the left side of the operator.
The reader should note the colors of codes,cooperated edge (green),breadth (yellow) and flash convex (blue).In wide area between flash convex and breadth is discharge chute,which is used to pile up the rest of the material,and can ensure the breadth out of compression or extrusion.If that happens,the dies cannot be closed tightly,which will
not be able to well control the thickness precision of forged connecting rods.In the forming forging die chamber (middle),please pay attention to the discharge chute in the internal flash convex of the connecting rod crank end,used to pile up the extra internal flash.In any case the discharge chute can be filled.The design of preforging chamber die will be a slightly thicker and narrower than finished forgings.Radius are generally bigger,and is advantageous to the metal flow.In this method,volume of preforging die chamber is larger than forming forging 1-2%,thus to minimize metal flow for the forming of forging die exterior,and according to the requirement of the force and the fight against energy,die wear also is greatly reduced.
Match the boundary function is to provide a datum for the manufacture of connecting rod dies.The datum will help you in positioning the die chamber at the top and bottom die position,and can ensure that the correct die handle parallel and locate the die chamber,so as to improve the die assembly accuracy,and can get very match forging and die without requirement of too much datum adjustment.
Yellow breadth is used to control the final thickness of forgings.It must be very suitable for forging hammer,in order to over time,the breadth is not out of shape.It must also be evenly distributed on the four quadrants of dies,so as to be in parallel between the dies.Use a blower to remove scale can not only improve the surface quality forged connecting rods,and it also can keep the mold 'moment in a better working condition.
Ajax-CECO# 14 die forging hammer is suitable for forging these forged connecting rods, its blow energy can reach 18.9kj.Blow energy in forging hammer forging is very important,because it can keep the metal flow during forging hammer blow deformation.The biggest force depends on the actual deformation.For small deformation,very large force will destroy mould and equipment.With the increase of deformation,the impact power cuts.The application of programmable forging hammer can minimize wear and tear of equipments,and improve energy utilization.
Die forging hammer is programmable and can be set in advance in order to facilitate a special program to produce a forged connecting rod.In the above programmable output part of forging,estimated blow energy of 3 times straightening needs to be 16.7 KJ.These blow energy can forge high deformation so that the resultant force is very low.Straightening machine is designed so that dies can be shut down under the final blow.It also ensures preforging die chamber can start work under the same shape.5 times preforging blow energy is 15.3 KJ,the purpose is that dies will close tightly in the last impact process,and then through a single blow,blow energy is 7.4 KJ,ensure mold tightly closed,thus ensuring a tight tolerance of forged connecting rods.So closed die forging hammer programming procedure is under 16.7 KJ blow energy hit three times,hit 5 times under 15.3 KJ blow energy,blow one under 7.4 KJ blow energy.In the first two working procedure,hit rate can be controlled,allowing to scale operation.Between different sequence (or die) between the chamber,the delay can be programmed,allows the operator to set the time in the operation between forging die chambers.If order interruption,such as a forging card in the dies,the operator has a few seconds time to handle this kind of situation,and then restart the forging sequence.If he didn't handle good,will alarm sound and program reset to start to order.
Die forging hammer and the control part as below:
Die forging process display includes a lot of useful data,information,and the programming information.The biggest advantages of programmable forging hammer is that it can standardize the production process.Standardization can be repetitive operation,the repeatability is capable of producing consistent forged connecting rods,guarantee the stability of the quality of forgings.Another benefit of forging hammer is the ability to constantly improve the amount of force to ensure dies closed,and it also can ensure the tightly closed between the die holders.Other forging method must use more elasticity machines to ensure that tension and deformation ability,this will lead too big forging size,cause the thickness tolerance out-of-tolerance when mass production,and result in taper phenomenon of forged connecting rods.
Conclusion
After forging,using a standard edge cutting press and die to trimming the connecting rod.After trimming,forged connecting rods as shown in the figure below.Pay attention to the lighter color of trimming section,thus a final and similar trimmed products produced,this finally greatly reduced the cost of connecting rod.
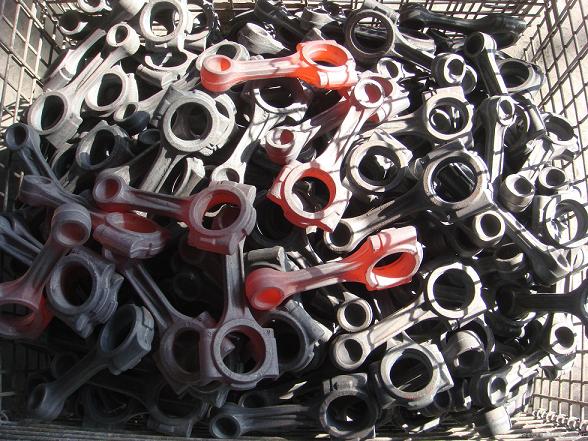
Forged connecting rods are regarded as the quality standards of internal combustion engine to use for decades.Over the years,production methods of connecting rods are constantly changed,includingforging hammer forging,press forging,metal powder forging and casting.In the early years of auto industry development,forging hammer forging is considered to be one of the best forging method.However,in the middle of the twentieth century,due to the higher requirements for quality and tolerance,the forging method must be changed,so manufacturers began to use mechanical press to replace forging hammer.The most effective way to reduce the manufacturing cost is to improve the material utilization.Increasingly stringent requirements for weight and size tolerance promotes the use of powder forging method.Another advantage in addtion to tolerance is that we could forge connecting rod cover toegther with connecting rod,and can open the cover from connecting rod,thus manufacturing cost can be saved.In the late twentieth century, forging method developed into "open" forged steel connecting rods(Why use steel for drop forged connecting rods in automotive cylinder engine?),it is also one of the strengths of the powder forging.The strength of forged steel connecting rod is higher than powder metallurgy rod.Increase as the engine compression ratio,compared with the powder forging connecting rod(wrought vs powder forged connecting rods),high strength of forged steel connecting rod becomes more satisfactory,this forging method can meet the both strict requirements of weight and size tolerance.
This paper mainly describes the modern production technology and die design method,this method is a very successful forging process.According to such forging process of connecting rods,statistical results show that the weight tolerance is less than 4g,thickness tolerance is less than +/-5mm.
Background
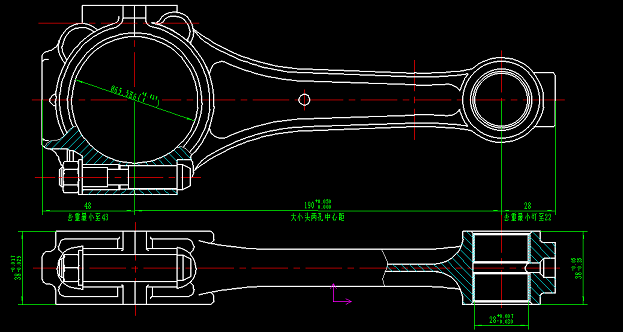
This forging part is a single part weighting 540 grams,the distance from the centerline of the connecting rod to the centerline is 129.6 mm (as shown in the figure below).Weight tolerance requirement of forged connecting rod in the drawing is +/-10g.Total thickness difference allows for +.4/-.2mm. Material of connecting rod is 40 Cr.
Process
Process design starts from using our CADIF (spreadsheet) program on the analysis of the forging process,CADIF program is to use a simplified geometry and material properties at high temperatures to estimate required equipment specifications,the quantities of the die chamber and the production efficiency.Here,we use AISI4140 as product material,and execute the # 14 die forging hammer (14000 ft-lb,19 kJ) analysis.CADIF input part of a display is as follows for your reference
After the assessment of the input,CADIF recommend a # 14 die forging hammer.Forging process will be 5 times preforging and 1 time forming forging.The estimated die life is for 20000pcs forged connecting rods.
Analysis can also estimate other process parameters like trimming tonnage,production efficiency and heating load.The optimal size of the induction heating power rating of 400-500kW.The generated output as shown below
You can now continue to push forward the design of dies,this design starts from forming materials distribution.Forming forging platter as shown in the figure below,like what we see from the picture,forging platter is designed as one module and two chambers,end to end,with the crank end embedded to enhance the platter.To some extent,the generated design depends on the method of forging.In this case,can use roller of cross wedge rolling mill to produce a circular cross section.Complete design of the platter as below model.
This operation is flattened in the forging hammer,in order to better distribute material,to better cover preforging die chamber.Die design using a multi-step straightening machine,such as mold pictures below.Straightening machine will be placed in the left side of the operator.
The reader should note the colors of codes,cooperated edge (green),breadth (yellow) and flash convex (blue).In wide area between flash convex and breadth is discharge chute,which is used to pile up the rest of the material,and can ensure the breadth out of compression or extrusion.If that happens,the dies cannot be closed tightly,which will
not be able to well control the thickness precision of forged connecting rods.In the forming forging die chamber (middle),please pay attention to the discharge chute in the internal flash convex of the connecting rod crank end,used to pile up the extra internal flash.In any case the discharge chute can be filled.The design of preforging chamber die will be a slightly thicker and narrower than finished forgings.Radius are generally bigger,and is advantageous to the metal flow.In this method,volume of preforging die chamber is larger than forming forging 1-2%,thus to minimize metal flow for the forming of forging die exterior,and according to the requirement of the force and the fight against energy,die wear also is greatly reduced.
Match the boundary function is to provide a datum for the manufacture of connecting rod dies.The datum will help you in positioning the die chamber at the top and bottom die position,and can ensure that the correct die handle parallel and locate the die chamber,so as to improve the die assembly accuracy,and can get very match forging and die without requirement of too much datum adjustment.
Yellow breadth is used to control the final thickness of forgings.It must be very suitable for forging hammer,in order to over time,the breadth is not out of shape.It must also be evenly distributed on the four quadrants of dies,so as to be in parallel between the dies.Use a blower to remove scale can not only improve the surface quality forged connecting rods,and it also can keep the mold 'moment in a better working condition.
Ajax-CECO# 14 die forging hammer is suitable for forging these forged connecting rods, its blow energy can reach 18.9kj.Blow energy in forging hammer forging is very important,because it can keep the metal flow during forging hammer blow deformation.The biggest force depends on the actual deformation.For small deformation,very large force will destroy mould and equipment.With the increase of deformation,the impact power cuts.The application of programmable forging hammer can minimize wear and tear of equipments,and improve energy utilization.
Die forging hammer is programmable and can be set in advance in order to facilitate a special program to produce a forged connecting rod.In the above programmable output part of forging,estimated blow energy of 3 times straightening needs to be 16.7 KJ.These blow energy can forge high deformation so that the resultant force is very low.Straightening machine is designed so that dies can be shut down under the final blow.It also ensures preforging die chamber can start work under the same shape.5 times preforging blow energy is 15.3 KJ,the purpose is that dies will close tightly in the last impact process,and then through a single blow,blow energy is 7.4 KJ,ensure mold tightly closed,thus ensuring a tight tolerance of forged connecting rods.So closed die forging hammer programming procedure is under 16.7 KJ blow energy hit three times,hit 5 times under 15.3 KJ blow energy,blow one under 7.4 KJ blow energy.In the first two working procedure,hit rate can be controlled,allowing to scale operation.Between different sequence (or die) between the chamber,the delay can be programmed,allows the operator to set the time in the operation between forging die chambers.If order interruption,such as a forging card in the dies,the operator has a few seconds time to handle this kind of situation,and then restart the forging sequence.If he didn't handle good,will alarm sound and program reset to start to order.
Die forging hammer and the control part as below:
Die forging process display includes a lot of useful data,information,and the programming information.The biggest advantages of programmable forging hammer is that it can standardize the production process.Standardization can be repetitive operation,the repeatability is capable of producing consistent forged connecting rods,guarantee the stability of the quality of forgings.Another benefit of forging hammer is the ability to constantly improve the amount of force to ensure dies closed,and it also can ensure the tightly closed between the die holders.Other forging method must use more elasticity machines to ensure that tension and deformation ability,this will lead too big forging size,cause the thickness tolerance out-of-tolerance when mass production,and result in taper phenomenon of forged connecting rods.
Conclusion
After forging,using a standard edge cutting press and die to trimming the connecting rod.After trimming,forged connecting rods as shown in the figure below.Pay attention to the lighter color of trimming section,thus a final and similar trimmed products produced,this finally greatly reduced the cost of connecting rod.