How to Increase Production with Drop Forging?
When it comes to manufacturing processes, there are a variety of techniques that can be used to produce high-quality parts and components. One such process is drop forging, which is a technique that is used to create strong and durable metal parts.
Drop forging is a manufacturing process that involves heating metal to a high temperature and then using a hammer or press to deform the metal into the desired shape. The process is called "drop forging" because the metal is dropped into the forging machine. The metal is typically heated to a temperature of around 2200 degrees Fahrenheit, which makes it more malleable and easier to shape. Once the metal is heated, it is placed in the forging machine, and the hammer or press is used to apply pressure to the metal, shaping it into the desired form.
Drop forging is often used to create parts and components for various industries, including automotive, aerospace, and construction. The process is known for producing parts that are strong, durable, and resistant to wear and tear. Drop forging is also cost-effective, making it a popular choice for manufacturers who want to produce high-quality parts without breaking the bank.
If you are looking to increase production with drop forging, there are several things you can do to get the most out of this manufacturing process. Here are some tips to consider:
Automate the process
One of the most effective ways to increase production with drop forging is to automate the process. Automation helps to reduce production time and labor costs. Automated drop forging machines can produce parts with high accuracy and consistency. Automation also reduces the risk of errors and accidents that may occur during manual drop forging.
Use High-Quality Materials
The quality of materials used in drop forging has a significant impact on the final product. Using high-quality materials such as steel alloys with high strength-to-weight ratios can help create parts with better performance and longer lifespans. High-quality materials also reduce the chances of defects and cracks that may occur during drop forging.
Increase Heat Treatment Capabilities
Heat treatment is an essential part of the drop forging process. It involves heating the metal to a specific temperature, then cooling it down to increase its strength and durability. Increasing the heat treatment capabilities of your drop forging facility can help improve the quality of your parts. Heat treatment can help produce parts with better mechanical properties and improved resistance to corrosion and wear.
Improve Production Planning
Improving production planning is essential to increasing production rates. Drop forging facilities can optimize production by creating efficient production plans. The plan should consider factors such as machine utilization, labor availability, material availability, and delivery times. A well-planned production process can help reduce downtime, increase efficiency, and reduce production costs.
Implement Lean Manufacturing Practices
Lean manufacturing is a methodology used to reduce waste and increase efficiency in production. Implementing lean manufacturing practices in drop forging can help identify and eliminate non-value-added activities. Lean manufacturing practices can help improve quality, reduce lead times, and increase production rates. It also helps improve safety and reduces the risk of accidents in the facility.
Use Computer-Aided Design (CAD) Software
CAD software can help improve the accuracy of the drop forging process. CAD software enables engineers to create 3D models of parts, allowing them to simulate the forging process and identify potential issues before the manufacturing process begins. CAD software can also help optimize the design of parts, reducing material usage and waste.
Train Employees
Training employees is essential to improving production rates with drop forging. Employees need to understand the drop forging process and how to operate the equipment correctly. Proper training can help reduce the risk of accidents and improve efficiency. Training can also help employees identify potential problems and find solutions quickly, reducing downtime.
CFS Forge is a leading drop forging manufacturer of high-quality drop forgings for a wide range of industries. With over 20 years of experience in the manufacturing industry, CFS Forge has the expertise and resources to provide you with the highest quality drop forgings available.
At CFS Forge, we use only the highest quality materials and the latest manufacturing techniques to produce drop forgings that are strong, durable, and reliable. Our team of experienced engineers and technicians work closely with our customers to ensure that every project is completed to their exact specifications and requirements.
We offer a wide range of drop forging services, including hot forging, cold forging, and warm forging. We can produce drop forgings in a wide range of materials, including carbon steel, alloy steel, stainless steel, and aluminum. We can also produce drop forgings in a wide range of shapes and sizes, from small, intricate parts to large, complex components.
In addition to our drop forging services, we also offer a range of value-added services, including CNC machining, heat treatment, and surface treatment. This means that we can provide you with a complete solution for your manufacturing needs, from initial design and engineering to final production and finishing.
If you are looking for a reliable and experienced partner for your drop forging production needs, contact CFS Forge today. We would be happy to discuss your project and provide you with a quote for our services
Drop forging is a manufacturing process that involves heating metal to a high temperature and then using a hammer or press to deform the metal into the desired shape. The process is called "drop forging" because the metal is dropped into the forging machine. The metal is typically heated to a temperature of around 2200 degrees Fahrenheit, which makes it more malleable and easier to shape. Once the metal is heated, it is placed in the forging machine, and the hammer or press is used to apply pressure to the metal, shaping it into the desired form.
Drop forging is often used to create parts and components for various industries, including automotive, aerospace, and construction. The process is known for producing parts that are strong, durable, and resistant to wear and tear. Drop forging is also cost-effective, making it a popular choice for manufacturers who want to produce high-quality parts without breaking the bank.
Tips for Increasing Production with Drop Forging
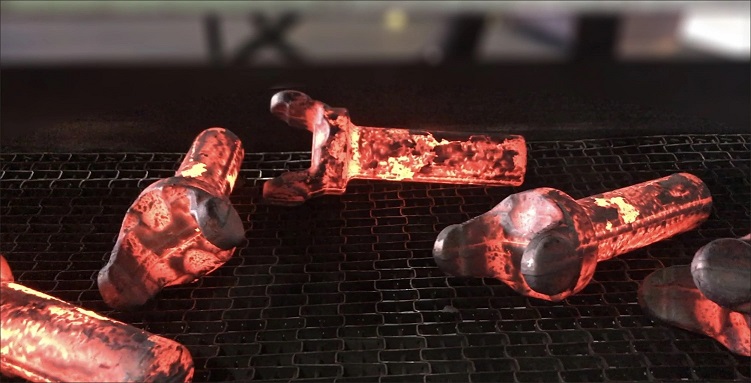
If you are looking to increase production with drop forging, there are several things you can do to get the most out of this manufacturing process. Here are some tips to consider:
Automate the process
One of the most effective ways to increase production with drop forging is to automate the process. Automation helps to reduce production time and labor costs. Automated drop forging machines can produce parts with high accuracy and consistency. Automation also reduces the risk of errors and accidents that may occur during manual drop forging.
Use High-Quality Materials
The quality of materials used in drop forging has a significant impact on the final product. Using high-quality materials such as steel alloys with high strength-to-weight ratios can help create parts with better performance and longer lifespans. High-quality materials also reduce the chances of defects and cracks that may occur during drop forging.
Increase Heat Treatment Capabilities
Heat treatment is an essential part of the drop forging process. It involves heating the metal to a specific temperature, then cooling it down to increase its strength and durability. Increasing the heat treatment capabilities of your drop forging facility can help improve the quality of your parts. Heat treatment can help produce parts with better mechanical properties and improved resistance to corrosion and wear.
Improve Production Planning
Improving production planning is essential to increasing production rates. Drop forging facilities can optimize production by creating efficient production plans. The plan should consider factors such as machine utilization, labor availability, material availability, and delivery times. A well-planned production process can help reduce downtime, increase efficiency, and reduce production costs.
Implement Lean Manufacturing Practices
Lean manufacturing is a methodology used to reduce waste and increase efficiency in production. Implementing lean manufacturing practices in drop forging can help identify and eliminate non-value-added activities. Lean manufacturing practices can help improve quality, reduce lead times, and increase production rates. It also helps improve safety and reduces the risk of accidents in the facility.
Use Computer-Aided Design (CAD) Software
CAD software can help improve the accuracy of the drop forging process. CAD software enables engineers to create 3D models of parts, allowing them to simulate the forging process and identify potential issues before the manufacturing process begins. CAD software can also help optimize the design of parts, reducing material usage and waste.
Train Employees
Training employees is essential to improving production rates with drop forging. Employees need to understand the drop forging process and how to operate the equipment correctly. Proper training can help reduce the risk of accidents and improve efficiency. Training can also help employees identify potential problems and find solutions quickly, reducing downtime.
Contact CFS Forge for Drop Forging Production
CFS Forge is a leading drop forging manufacturer of high-quality drop forgings for a wide range of industries. With over 20 years of experience in the manufacturing industry, CFS Forge has the expertise and resources to provide you with the highest quality drop forgings available.
At CFS Forge, we use only the highest quality materials and the latest manufacturing techniques to produce drop forgings that are strong, durable, and reliable. Our team of experienced engineers and technicians work closely with our customers to ensure that every project is completed to their exact specifications and requirements.
We offer a wide range of drop forging services, including hot forging, cold forging, and warm forging. We can produce drop forgings in a wide range of materials, including carbon steel, alloy steel, stainless steel, and aluminum. We can also produce drop forgings in a wide range of shapes and sizes, from small, intricate parts to large, complex components.
In addition to our drop forging services, we also offer a range of value-added services, including CNC machining, heat treatment, and surface treatment. This means that we can provide you with a complete solution for your manufacturing needs, from initial design and engineering to final production and finishing.
If you are looking for a reliable and experienced partner for your drop forging production needs, contact CFS Forge today. We would be happy to discuss your project and provide you with a quote for our services