How does Forging Affect Grain Structure?
What is grain structure? Grain flow is a directional orientation of metal grains and any inclusions that have been deformed by forging. Individual grains are elongated in the direction of the metal flow or plastic deformation. More importantly, nonmetallic inclusions, particles and other imperfections inherited from the casting process (forging vs casting) are elongated in the direction of grain flow. It should be noted that grain flow occurs to some degree in all metal-forming processes, not just forging. As a professional forging manufacturer, this article we would like to discuss how forging affects grain structure.
Grain flow is one of the major benefits by the use of forgings. Unfortunately, there are misconceptions on the topic, which include the underlying causes of grain flow, the benefits that can be accrued from grain flow and how to achieve an optimum grain flow. In the best case, grain flow results in more application of forgings, especially for some critical applications when safety and strength is considered.
Figure 1. Grain flow is observed in this sliced section of a forging. It has been cut, polished and etched with an acid solution. The observed flow lines are due primarily to the particles and inclusions, which were remnants of the original casting. These have been deformed during the billet conversion and forging process. The forging process has also aligned the grains of the metal in a direction similar to the flow lines in this picture.
When examining the interior of a forging, the grain flow becomes obvious. Figure 1 shows the grain flow in a forged and machined component. The observation of the grain flow in this figure requires some special preparation methods. After the forging has been sectioned, it needs to be ground and polished similar to a metallographic sample. The major difficulty with this step in the process is that forgings are usually substantially larger in size than small samples for metallographic analysis. Care must be taken in the preparation to ensure that the surface is flat and not beveled. After polishing is completed, an etchant (a solution with acid) is applied to the polished surface.
The important implication about grain flow is that some mechanical properties vary with respect to orientation relative to grain flow. This fact is one of the major advantages of forging. This variation in mechanical properties can be exploited so that the actual product has superior properties in a critical direction relative to those expected from the alloy composition itself.
However, we should be clear that not all of the mechanical properties will vary significantly with the grain flow. For example, strength and hardness are primarily controlled by the alloy chemistry and the heat treatment that is given to the forging. Grain flow will not have a major effect on the strength or the hardness of the alloy. In contrast, desirable properties associated with retarding crack propagation can see significant differences depending on the grain flow and the direction of the moving crack. So, properties like fatigue strength, impact toughness and ductility, which are measures of a material’s resistance to cracking (measured after fracture), can be significantly improved if the crack propagation direction and the grain flow are properly aligned. The optimum alignment occurs when the maximum principal stress (perpendicular to a potential crack or fracture) is aligned with the grain-flow lines.
When the properties of a metal are independent of direction, the material is described as being isotropic. Plastically deformed metals with grain flow have anisotropic properties. Figure 2. This illustrates illustration depicts anisotropic properties that are dependent on the grain-flow direction. The test samples that are machined from the plastically deformed block are (left to right) longitudinal, transverse and short transverse, respectively. Note the major increase in properties that are associated with a crack/fracture formation and propagation through the test sample. The yield strength is reasonably constant.
Grain flow is one of the major benefits by the use of forgings. Unfortunately, there are misconceptions on the topic, which include the underlying causes of grain flow, the benefits that can be accrued from grain flow and how to achieve an optimum grain flow. In the best case, grain flow results in more application of forgings, especially for some critical applications when safety and strength is considered.
How Grain Flows in Forging Process?
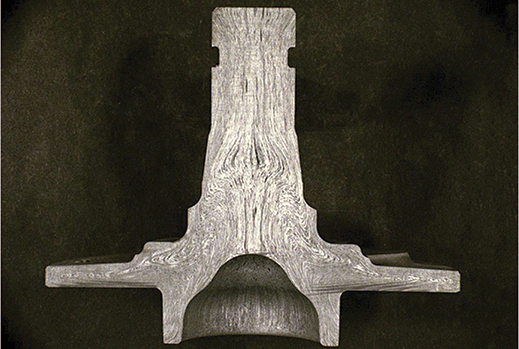
When examining the interior of a forging, the grain flow becomes obvious. Figure 1 shows the grain flow in a forged and machined component. The observation of the grain flow in this figure requires some special preparation methods. After the forging has been sectioned, it needs to be ground and polished similar to a metallographic sample. The major difficulty with this step in the process is that forgings are usually substantially larger in size than small samples for metallographic analysis. Care must be taken in the preparation to ensure that the surface is flat and not beveled. After polishing is completed, an etchant (a solution with acid) is applied to the polished surface.
Effects of Grain Structure on Forging
The important implication about grain flow is that some mechanical properties vary with respect to orientation relative to grain flow. This fact is one of the major advantages of forging. This variation in mechanical properties can be exploited so that the actual product has superior properties in a critical direction relative to those expected from the alloy composition itself.
However, we should be clear that not all of the mechanical properties will vary significantly with the grain flow. For example, strength and hardness are primarily controlled by the alloy chemistry and the heat treatment that is given to the forging. Grain flow will not have a major effect on the strength or the hardness of the alloy. In contrast, desirable properties associated with retarding crack propagation can see significant differences depending on the grain flow and the direction of the moving crack. So, properties like fatigue strength, impact toughness and ductility, which are measures of a material’s resistance to cracking (measured after fracture), can be significantly improved if the crack propagation direction and the grain flow are properly aligned. The optimum alignment occurs when the maximum principal stress (perpendicular to a potential crack or fracture) is aligned with the grain-flow lines.
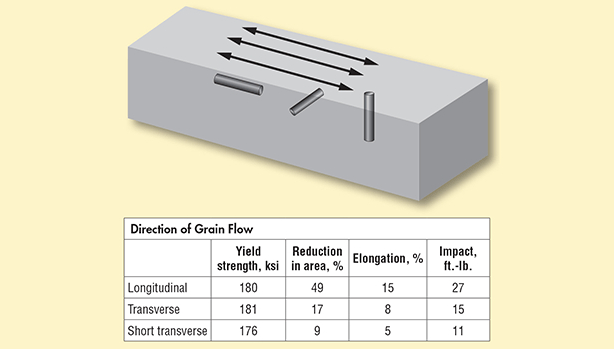