Forging
Forging Definition and Development

As one of the oldest metalworking process, there is a long histoty of forging technique. At the beginning of forging process, it was performed by a smith using hammer and anvil, through introducing water power to the production and working of iro. In the 12th century, allowed the use of large trip hammers or power hammers that exponentially increased the amount and size of iron that could be produced and forged easily. The smithy or forge has evolved over centuries to become a facility with engineered processes, production equipment, tooling, raw materials and products to meet the demands of modern industry.
Nowadays, modern metal forging is operated either with presses or with hammers powered by compressed air, electricity, hydraulics or steam. These hammers may have reciprocating weights in the thousands of pounds. Smaller power hammers, 500 lb (230 kg) or less reciprocating weight, and hydraulic presses are common in art smithies as well. Some steam hammers remain in use, but they became obsolete with the availability of the other, more convenient, power sources.
Why Forging (Forging vs Casting) ?
Compared with cast or machined part, metal forging can produce a piece with higher strength. During the metal shaping process, its internal grain deforms to follow the final shape of the part. As a result, the grain is continuous throughout the part, giving rise to a piece with improved strength characteristics. Besides, unlike pouring, high pressure to forge parts will make compact inner structure, and it will not easy to produce inner defects.
Secondly, when compared to casting or fabrication, forging can offer a lower total cost in a more cost-effective way. When you take all the costs that occured from procurement to lead time to rework into consideration, then factor in the costs of scrap, downtime and further quality issues, forging can win the long-term benefits that can outweigh castings or fabrications that might offer short-term cost-savings.
Thirdly, forging can offer a short production cycle. When forging, if the shape is not quite complex, it can be just one-time forged, in just few seconds, and then trimmed to get finished part. So in general, we can finish production in a short production cycle within 20 days.
Next, compared with casting, metals after forging can improve its organizational structure and mechanical properties. Casting organization after forging method, due to metal deformation and recrystallization, make original bulky dendrite and columnar grain to fine grain and uniform axial recrystallization organization, make original segregation, porosity, slag compaction in the steel ingot rammed and welded, thus to make its organization become more closely, and improve the plasticity and mechanical properties of the metal.
Metal Forging Materials
Steel Forging: Main materials of forging are forged steel, such steel could be carbon steel, alloy steel and stainless steel. Stainless steel is the most expensive material in forging for its special material characteristics. Normally such steels are all improted from domestic material factories in round bar shape. And each material specification can have different diameters to better suit the shape of forgings. Common steel specifications are 20#, 35#, 45#, 20Cr, 40Cr, 20CrMnTi, 20CrMo, 30CrMo, 35CrMo, 42CrMo, Q235, Q345, A105, etc.
Aluminum Forging: Aluminum is used in metal forging for its lightweight. High-strength aluminium alloys have the tensile strength of medium strong steel alloys while providing significant weight advantages. Therefore, aluminium forged parts are mainly used in aerospace, automotive industry and many other fields of engineering especially in those fields, where highest safety standards against failure by abuse, by shock or vibratory stresses are needed. Such parts are for example chassis parts, steering components and brake parts. Commonly used alloys are AlSi1MgMn (EN AW-6082) and AlZnMgCu1,5 (EN AW-7075). About 80% of all aluminium forged parts are made of AlSi1MgMn. The high-strength alloy AlZnMgCu1,5 is mainly used for aerospace applications.
Copper Forging: Copper forgings are ideal for applications where high electrical and thermal conductivity is desirable. There are many durability benefits to using copper forgings that come from closed-die forming. This includes the optimization of microstructural characteristics of copper by applying a range of forging temperatures and annealing cycles that improve structural properties.
To meet large demands of forgings and ensure our production capacities, we have a special material warehouse to stock different steel bars. And to distinguish different material specifications, they are marked with different colours.
Metal Forging Process and Types
Different forging methods have a different process, we generally divide metal forging processes into open die forging and closed die forging.
Open Die Forging: Also known as smith forging. In open-die forging, a hammer strikes and deforms the workpiece, which is placed on a stationary anvil. Open die forging gets its name from the fact that the dies (the surfaces that are in contact with the workpiece) do not enclose the workpiece, allowing it to flow except where contacted by the dies. The operator therefore needs to orient and position the workpiece to get the desired shape. The dies are usually flat in shape, but some have a specially shaped surface for specialized operations. For example, a die may have a round, concave, or convex surface or be a tool to form holes or be a cut-off tool. Open-die forgings can be worked into shapes which include discs, hubs, blocks, shafts (including step shafts or with flanges), sleeves, cylinders, flats, hexes, rounds, plate, and some custom shapes. Open-die forging lends itself to short runs and is appropriate for art smithing and custom work. In some cases, open-die forging may be employed to rough-shape ingots to prepare them for subsequent operations. Open-die forging may also orient the grain to increase strength in the required direction.
Closed Die Forging: Also called impression die forging. In closed die forging, the metal is placed between upper and lower dies, which are attached to an anvil. The hammer is then dropped on the workpiece, causing the metal to flow and fill the die cavities. The hammer is generally in contact with the workpiece at the speed of milliseconds. Depending on the size and complexity of the part, the hammer may be dropped multiple times in quick succession. Excess metal is squeezed out of the die cavities, forming what is referred to as "flash". The flash cools more rapidly than the rest of the material, and is stronger than the metal in the die, so it helps prevent more flash from forming. This also forces the metal to completely fill the die cavity. After forging, the flash is removed. In commercial closed die forging, the workpiece is usually moved through a series of cavities in a die to get from an ingot to the final shape. The first forging is used to distribute the metal into the rough shape in accordance to the needs of later cavities; this impression is called an "edging", "fullering", or "bending" impression. The following cavities are called "blocking" cavities, in which the piece is working into a shape that more closely resembles the final product. These stages usually impart the workpiece with generous bends and large fillets. The final shape is forged in a "final" or "finisher" impression cavity. If there is only a short run of parts to be done, then it may be more economical for the die to lack a final impression cavity and instead machine the final features. Closed die forging has been improved in recent years through increased automation which includes induction heating, mechanical feeding, positioning and manipulation, and the direct heat treatment of parts after forging. One variation of closed die forging is called "flashless forging", or "precision forging". In this type of forging, the die cavities are completely closed, which keeps the workpiece from forming flash. The major advantage to this process is that less metal is lost to flash. Flash can account for 20 to 45% of the starting material. The disadvantages of this process include additional cost due to a more complex die design and the need for better lubrication and workpiece placement. Closed-die forging has a high initial cost due to the creation of dies and required design work to make working die cavities. However, it has low recurring costs for each part, thus forgings become more economical with more volume. This is one of the major reasons closed-die forgings are often used in the automotive and tool industries. Another reason forgings are common in these industrial sectors is that forgings generally have about a 20 percent higher strength-to-weight ratio compared to cast or machined parts of the same material.
Generally speaking, open die forging is designed for large metal components, and closed die forging is mainly for small precision parts, see more about differences between closed die forging and open die forging......
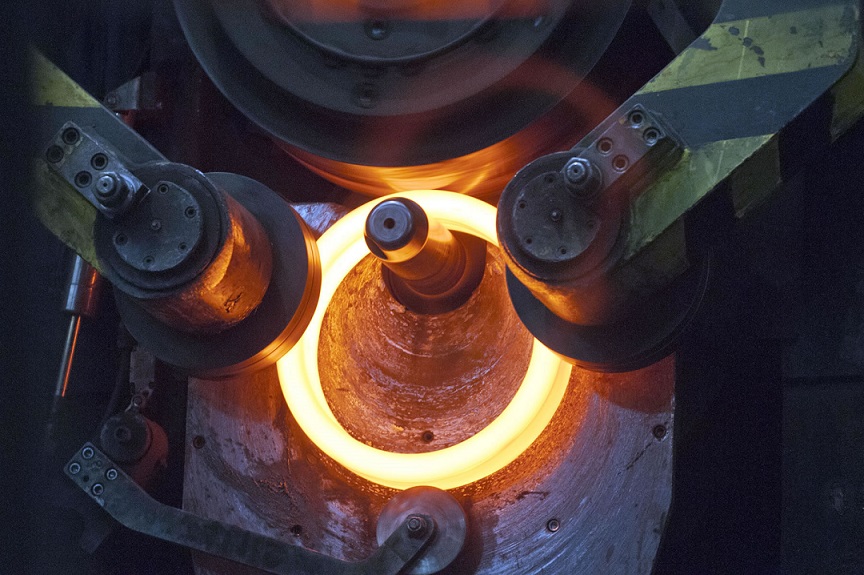
Roll Forging: Roll forging is a kind of forging technique that shapes a metal part by opposing rolls. Although rolls are used to deform the shape of raw material, it still belongs to metal forging process, other than rolling process. It is more similar to metal forging than metal rolling, as this is a discrete process, not a continuous one. Like other forging process, roll forging starts from heating the billet. The precisely shaped geometry of grooves on the roll, forge the part to the desired dimensions. The forging geometry of the rolls used to forge metal parts is only present over a portion of the roll's circumference. Only part of a full revolution of a roll is needed to forge the work piece. Typically in manufacturing industry, the forging geometry on the rolls may occupy from one quarter to three quarters of the roll's circumference. Roll forging process is often used to make all kinds of rings, flanges as well as other parts. Parts created by roll forging possess superior mechanical properties than those produced from many other processes.
Application of Metal Forgings
As one of the main metal processing process,applications of forgings are so wide. Such forgings are mostly used by people when safety factor is considered and good mechanical properties are needed. So forgings can be used in different industries as listed in below:
- Automotive: Forging is extensively used in the automotive industry to produce components such as connecting rods, crankshafts, gears, wheel hubs, axles, and suspension parts. These components require high strength and durability, which forging can provide.
- Aerospace: The aerospace industry relies on forging to create parts that can withstand extreme stress and high temperatures. Examples include turbine blades, engine mounts, landing gear components, and structural parts for aircraft fuselages and wings.
- Agriculture: Forging is used to create durable and wear-resistant components for agricultural equipment, such as tractor parts, plowshares, and cultivator tines.
- Oil and Gas: Forged parts are commonly found in the oil and gas industry due to their ability to withstand high pressures and temperatures. Examples include flanges, valves, and fittings for pipelines, drilling equipment, and refinery components.
- Construction: Forged parts are essential in construction equipment like cranes, excavators, and bulldozers. Components such as gears, shafts, and hooks are often made using the forging process.
- Defense: The defense industry uses forging to create essential components for vehicles, aircraft, and weaponry. Forged parts are often used in tanks, armored vehicles, gun barrels, and missile components due to their strength and durability.
- Hand tools: Many hand tools, such as wrenches, hammers, and pliers, are made using forging to ensure their durability and long-lasting performance.
- Power generation: Components for power generation equipment, including wind turbines, hydroelectric power stations, and nuclear reactors, often utilize forging to create parts that can withstand high stresses and operating conditions.
- Marine: Forged parts are found in various marine applications, including shipbuilding and offshore structures. Examples include propeller shafts, rudder components, and anchor chains.
- Railways: The railway industry uses forging to create components like axles, wheels, and couplings, which require high strength and durability to withstand the demanding conditions of railway operations.
Forging Company in China
CFS Forge began its forging business in 1998. Since then, we have steadily grown to be a leader in forging industry, and are well known for our engineering and service excellence. As one of the largest Chinese forging factories, CFS Forge is the one-stop forging company from forging dies developing to forging, machining, heat treatment and surface treatment. We can supply both forging blanks and machined forgings for your selection.
Today, CFS Forge employs about 150 people in our facilities, with over 8 forging production lines. Besides, we are also equipped with die & tool workshop, machining workshop for finished products and assemblies. We work jointly with customers in each market to develop product advancements that have led to products with extreme reliability and increased useful life. Whether looking for just a forging, or a finished component solution, we are sure the right partners for your project.
Any project in forging, pls contact us right now. You will be satisfied with our quality, price and service!