Forged Tie Rod Ends for Automotive Steering System
What are Tie Rod Ends?
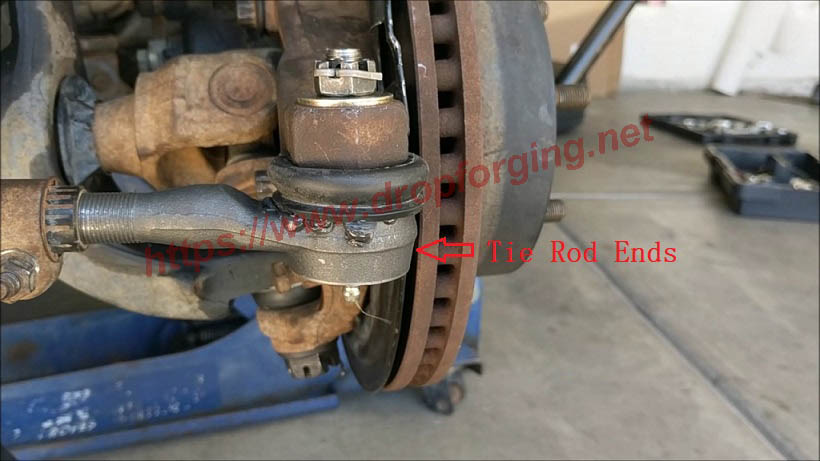
There are two types of tie rod ends - inner and outer. The inner tie rod ends are attached to the steering rack, while the outer tie rod ends connect the inner tie rod ends to the steering knuckle. Together, they ensure the driver can steer the vehicle accurately and smoothly.
However, tie rod ends are subjected to constant stress and can wear down over time, leading to steering problems. Therefore, the manufacturing process of these parts becomes critical to ensure they are robust, reliable, and durable. Among various manufacturing methods, the drop forging process is an ideal process in the automotive industry, which can enhance the tie rod end's strength and durability.
The Forging Material: AISI 1045 Steel / EN8 Mild Steel
AISI 1045 steel, the equivalent forging grade EN8 steel, is a medium strength steel with good tensile strength. This type of mild steel is generally tougher and stronger than standard mild steel, making it an excellent choice for numerous applications, including the manufacture of tie rod ends.
1045 steel's superior strength and toughness make it ideal for withstanding the heavy wear and tear that tie rod ends are subjected to in an automotive steering system. Moreover, 1045 steel has excellent machinability, which allows it to be easily shaped and finished to the exact specifications required for tie rod ends.
The combination of strength, toughness, and machinability makes mild steel AISI 1045 steel an excellent material for forged tie rod ends. Its properties ensure that the tie rod ends can provide reliable, long-lasting performance even in demanding conditions.
The Drop Forging Process of Tie Rod Ends
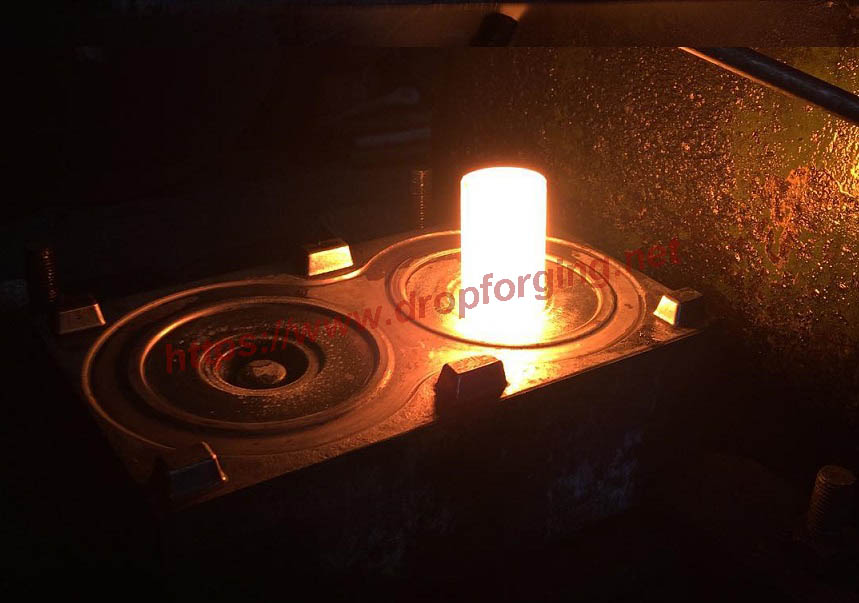
Here are the steps of forging tie rod ends at CFS Foge for automotive steering system:
- Material Selection: The initial stage involves selecting the appropriate material, which is typically steel due to its high strength, durability, and resistance to wear and tear.
- Heating: The selected material is heated to a specific temperature that makes it malleable and more accessible to work with.
- Forging: The heated material is then moved to a forging press. The press uses high pressure to shape the steel into the desired tie rod end shape. There are two primary types of forging: open-die and closed-die forging. In the manufacuring of tie rod ends, closed-die forging process, also known as impression-die forging, is commonly used. The heated steel is placed in a die that contains a cavity in the shape of the tie rod end. The press applies a force that pushes the steel into the die cavity, thus forming the tie rod end.
- Trimming and Finishing: After forging, the excess material (flash) that flowed outside the die cavity is trimmed off. The piece is then subjected to a finishing process, which may include sanding, grinding, or polishing, to achieve the necessary surface finish.
- Heat Treatment: The forged tie rod end is then heat-treated to enhance its hardness and strength. This process may involve normalizing, hardening, and tempering. Normalizing relieves internal stresses and refines the grain structure. Hardening increases hardness and strength, while tempering improves toughness and reduces brittleness.
- Inspection: The final step involves a thorough inspection of the tie rod end. This ensures that it meets the necessary dimensional accuracy, surface finish, and mechanical properties required for optimal performance and safety.
Why Forging for Tie Rod Ends Manufacturing?
Selecting the right manufacturing process for tie rod ends is a critical decision, which can significantly influence the parts' quality, durability, and performance. Over the years, drop forging has been considered as a preferred method for manufacturing tie rod ends. The advantages of forged tie rod ends include:
Strength and Durability
The forging process involves the use of high pressure and temperature to shape the metal, aligning its grain structure with the part's shape. This structural alignment results in a component with superior strength and increased resistance to wear and tear, compared to those produced using other manufacturing methods. Therefore, forged tie rod ends are more robust and durable, capable of withstanding the extreme stress and friction experienced in a car's steering system.
High Precision and Accuracy
Forging enables the production of parts with high dimensional accuracy and consistency. In closed-die forging, the heated metal is forced into a die cavity that closely mirrors the final component's shape. This results in tie rod ends with precise dimensions and minimal need for subsequent machining, ensuring a better fit in the vehicle's steering system.
Improved Reliability
The improved strength, durability, and precision of forged tie rod ends contribute to enhanced reliability of the vehicle's steering system. As these components are crucial for safe steering and maintaining wheel alignment, their reliability directly impacts the vehicle's safety and performance.
Cost Efficiency
Although the initial setup costs for forging can be high, it proves cost-effective in the long run, especially for mass production. Forging produces less waste material compared to other processes like casting or machining. Additionally, it reduces the need for secondary finishing operations, thereby saving time and resources.
CFS Forge: Your Reliable Manufacturer for Custom Forged Tie Rod Ends
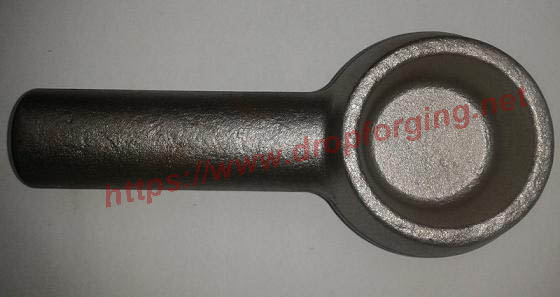
Choosing a reliable manufacturer is critical when it comes to sourcing quality forged steel tie rod ends. There are a lot of reasons why you should choose CFS Forge for custom forged tie rod ends manufacturing:
- Advanced Forging Equipments: Equipped with advanced forging equipments ranging from 300 tons to 2,500 tons, CFS Forge is capable of producing high-quality tie rod ends in different sizes. This capacity allows them to meet diverse needs, from small-scale to large-volume production runs.
- Strict Quality Control Procedure: At CFS Forge, quality isn't just a goal; it's a process. Our company follows a strict quality control procedure to ensure that every product meets or exceeds our customers' expectations. Furthermore, we provide comprehensive testing reports, including Production Part Approval Process (PPAP) files, giving customers full visibility into the quality and integrity of their tie rod ends.
- Custom Solutions: Due to the unique demands of each client, we provide custom forging solutions for different types of forged tie rod ends, allowing them to manufacture tie rod ends that perfectly match the specifications and performance requirements of our customers.
- Competitive Pricing: Despite the high-quality products, CFS Forge also maintains competitive pricing. This balance of cost and quality ensures that customers receive top-tier tie rod ends that deliver excellent performance and value for money.
- Excellent Customer Service: CFS Forge takes pride in its customer-centric approach, providing excellent customer service at every step. Whether it's a query, a concern, or a need for technical assistance, our team is always ready to help, ensuring a seamless and satisfying customer experience.