Forged Ball Joint Housings for Automotive Suspension System
Ball joint housings are key components within the automotive suspension system. They act as protective encasements for the ball joints, which are pivotal connections that link the control arms of the vehicle to its steering knuckles. The ball joint, securely housed, allows for a controlled and smooth range of motion between these components. This functionality is critical for effectively navigating bumps and making turns while driving.
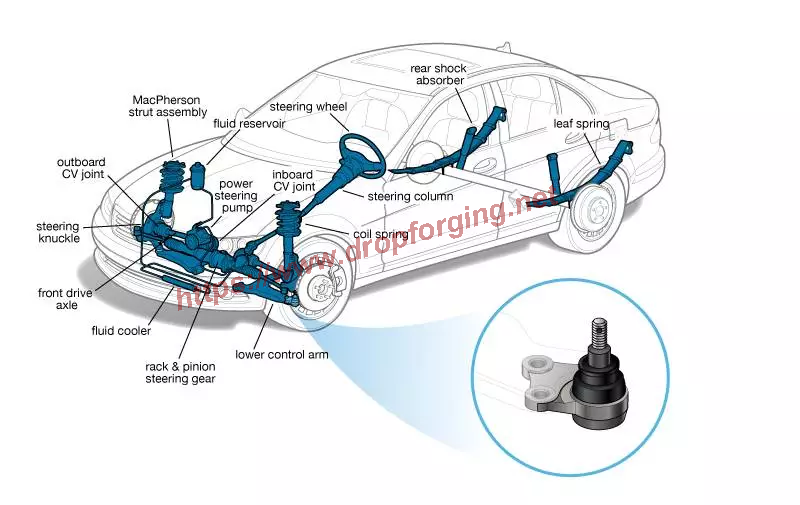
The role of the housing is not only to encase the ball joint but also to maintain its correct positioning even during high-intensity vehicular movements. Given the stress they endure and the crucial role they play in the suspension system, ball joint housings must be manufactured from materials that offer superior strength and durability. The quality and integrity of these housings can significantly impact the overall efficiency, performance, and lifespan of a vehicle's suspension system.
Drop forging is a suitable manufacturing process for ball joint housings. Forging delivers a range of benefits in the production of ball joint housings, particularly due to the process's ability to significantly enhance the properties and performance of the manufactured component. As a reliable drop forging manufacturer in China, CFS Forge can custom forge all types of ball joint housings to meet your drawing's specifications.
Material choice is a critical factor in the manufacturing of automotive components, and forged steel is widely recognized as one of the best options for producing ball joint housings. Forged steel is steel that has been heated and then hammered, pressed, or rolled under high pressure into a final shape, resulting in a highly durable and resilient product.
The key characteristics of forged steel that make it an ideal material for ball joint housings include:
The drop forging process for ball joint housing ensures the production of high-quality, durable, and reliable components. The resulting product benefits from the aligned grain structure of the steel, providing superior strength, increased toughness, and improved wear resistance - all critical properties for parts of an automotive suspension system. The steps involved in this process are outlined below:
Besides Ball joint housings, CFS Forge can also produce other forged steel automotive parts include:
When it comes to sourcing high-quality forged parts like forged steel ball joint housings, CFS Forge stands out as a reliable, reputable, and preferred drop forging manufacturer. As an industry leader with decades of experience in forging, CFS Forge is committed to delivering superior quality components that meet the stringent requirements of the automotive industry.
Here are several reasons to choose CFS Forge for your ball joint housings needs:
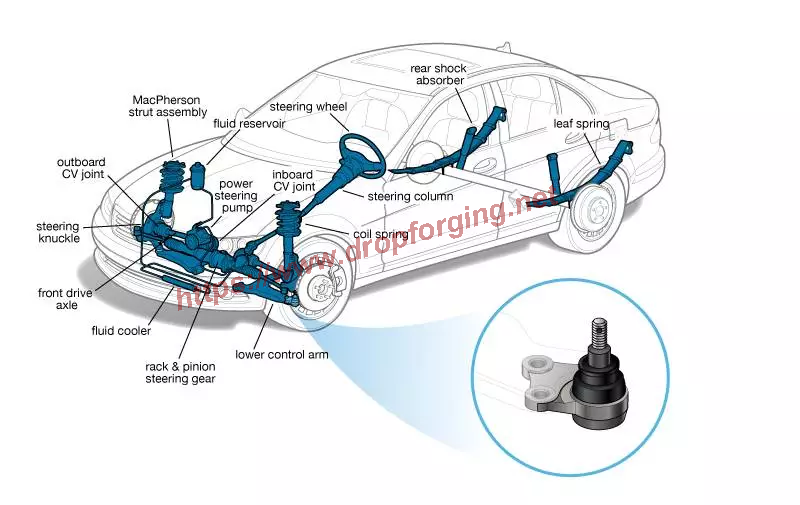
The role of the housing is not only to encase the ball joint but also to maintain its correct positioning even during high-intensity vehicular movements. Given the stress they endure and the crucial role they play in the suspension system, ball joint housings must be manufactured from materials that offer superior strength and durability. The quality and integrity of these housings can significantly impact the overall efficiency, performance, and lifespan of a vehicle's suspension system.
Drop forging is a suitable manufacturing process for ball joint housings. Forging delivers a range of benefits in the production of ball joint housings, particularly due to the process's ability to significantly enhance the properties and performance of the manufactured component. As a reliable drop forging manufacturer in China, CFS Forge can custom forge all types of ball joint housings to meet your drawing's specifications.
Material: Forged Steel
Material choice is a critical factor in the manufacturing of automotive components, and forged steel is widely recognized as one of the best options for producing ball joint housings. Forged steel is steel that has been heated and then hammered, pressed, or rolled under high pressure into a final shape, resulting in a highly durable and resilient product.
The key characteristics of forged steel that make it an ideal material for ball joint housings include:
- Superior Strength: Forged steel boasts exceptional strength, largely due to the realignment of its grain structure during the forging process. This realignment enhances its mechanical properties, making the resulting component more robust and capable of withstanding significant stress without deformation or failure.
- High Toughness and Durability: Forged steel components are incredibly tough and durable. They resist wear and tear, withstand high pressure and extreme temperatures, and are resistant to fatigue, making them well-suited to the demanding conditions that ball joint housings are exposed to in a vehicle's suspension system.
- Enhanced Metallurgical Properties: The forging process refines the grain structure of the steel and reduces structural defects, leading to improved metallurgical properties. This results in a more uniform and consistent material, contributing to the overall reliability and longevity of the forged component.
- Cost-effectiveness: Despite its superior properties, forged steel is relatively cost-effective, especially when considering the lifespan and performance benefits it offers. This makes it a practical choice for the manufacturing of high-performance automotive components like ball joint housings.
- Malleability: Steel becomes malleable at high temperatures, which allows it to be easily shaped during the forging process. This characteristic enables the creation of complex shapes and designs, such as those often required for ball joint housings.
Drop Forging Process for Ball Joint Housings at CFS
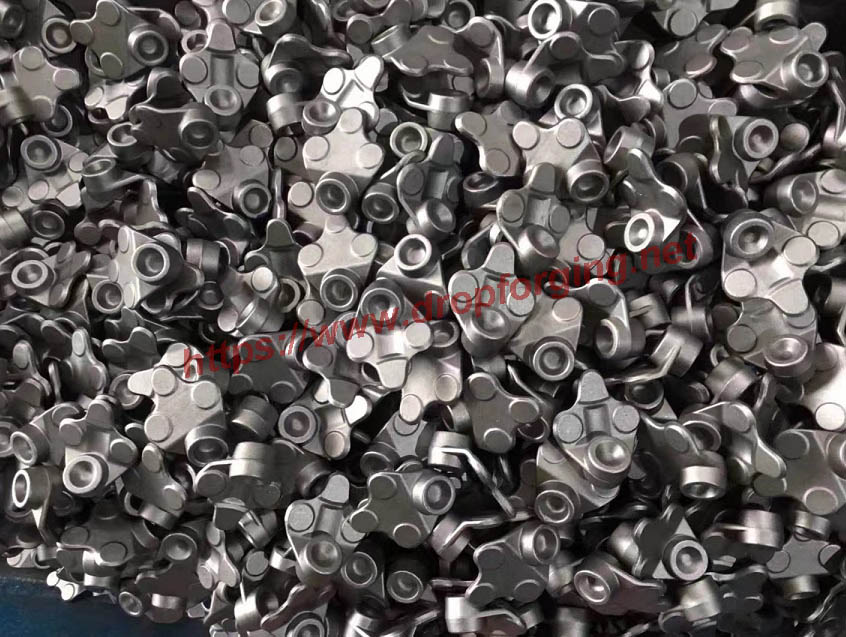
- Designing and Creating the Die: The first step in the drop forging process is the creation of a die, which is essentially a metal block that is used as a mold for shaping the forged part. This die is designed to match the exact dimensions and shape of the ball joint housing.
- Heating the Steel: The steel billet that will be used to create the ball joint housing is heated until it reaches a malleable state. The temperature needs to be controlled accurately to ensure the steel can be shaped effectively without melting or creating structural issues.
- Forging the Heated Steel: The heated steel is then placed in the drop forge machine, where it is subjected to high pressure exerted by a hammer or a press. This pressure "drops" the steel into the die, forcing it to take on the die's shape.
- Trimming and Finishing: Once the forging process is complete, the newly formed ball joint housing is removed from the die. Excess material, known as flash, is often formed around the edges of the part during forging. This flash is trimmed off, and the part may undergo additional finishing processes to achieve the desired surface finish and meet precise dimensional specifications.
- Heat Treatment: After forging and finishing, the ball joint housing often undergoes a heat treatment process. This step involves heating and cooling the part under controlled conditions to enhance certain properties, such as hardness, strength, and resistance to wear.
- Inspection and Quality Control: The final step in the process is a comprehensive inspection and quality control process to ensure the forged ball joint housing meets all required specifications and quality standards. This might include dimensional checks, surface quality inspection, and testing of mechanical properties.
Other Forged Steel Automotive Parts We Serve
Besides Ball joint housings, CFS Forge can also produce other forged steel automotive parts include:
- Forged Steel Connecting Rod
- Forged Steel Yoke Ends
- Forged Steel Steering Yokes
- Forged Steel Steering Knuckle
- Forged Steel Rocker Arm
- Forged Steel Wheel Hub
- Forged Steel Control Arm
- Forged Steel Tie Rod Ends
Contact CFS Forge for Custom Forging Solutions
When it comes to sourcing high-quality forged parts like forged steel ball joint housings, CFS Forge stands out as a reliable, reputable, and preferred drop forging manufacturer. As an industry leader with decades of experience in forging, CFS Forge is committed to delivering superior quality components that meet the stringent requirements of the automotive industry.
Here are several reasons to choose CFS Forge for your ball joint housings needs:
- ISO 9001 & TS 16949 Certified: CFS Forge operates under the ISO 9001 & TS 16949 certifications, affirming its adherence to international quality management principles and stringent quality control measures.
- Advanced Forging Equipments: With advanced forging equipments up to 2,500 tons, CFS Forge has the capability to produce all types of forged steel automotive parts, from small to large production runs, ensuring you receive your order in a timely manner.
- Strict Quality Control Procedure: CFS Forge prides itself on its rigorous quality control procedures. Each product undergoes a thorough inspection and testing process to ensure it meets all specifications and performance requirements. Testing reports, including PPAP files, can be provided for customer review and satisfaction.
- Custom Solutions: CFS Forge offers custom forging solutions to meet your unique requirements. Our expert team works closely with you to understand your needs and develop custom ball joint housings that perfectly fit your specifications.
- Competitive Pricing: Despite their commitment to superior quality, CFS Forge maintains competitive pricing, ensuring you receive top-notch products that offer excellent value for your investment.
- Excellent Customer Service: At CFS Forge, customer satisfaction is a top priority. Our dedicated customer service team is always ready to assist with your queries, concerns, and requests, providing a seamless and satisfying customer experience from start to finish.