Factors to Consider During Hot Forging Process
As the name suggests, the process of hot forging requires the heating of the metal, so the heating temperature has a significant impact on the forming process and result. In order to ensure the forgability of the metal and obtain good internal structure performance, the forging heating must follow certain heating specifications and carry out the forging process within the specified temperature. At the same time, because the temperature of the blank metal is very high, sometimes the mold also needs preheating, so there are certain requirements for the life of the mold and forming equipment. In order to ensure the progress of the forging process, the following major issues need to be considered during hot forging process:
1. Control of Pre-Forging Heating
In hot forging, the metal blank is heated to a certain temperature before forging. Can reduce the strength of the metal limit b sigma, improve its plasticity, and the higher the heating temperature, the greater the b sigma reduction, the required forming force is lower. In order to reduce the forming force and energy consumption, the heating temperature of the metal blank should be raised as far as possible on the premise of avoiding the occurrence of overburning of the metal. As the aluminum forging temperature range is narrow, so we should pay more attention to the control of pre-forging heating.
2. Lubrication During Deformation
In the forging process, the lubrication between the die and the blank is closely related to the forging quality, the forming load and the life of the die. When the lubrication is poor, the friction coefficient increases, the metal material in the mold chamber fluidity is poor. When the lubrication is good, the smaller the friction coefficient, is conducive to the flow of metal materials fill. The influence of friction coefficient on forging is twofold. On the one hand, the increase of friction force can increase the resistance at the bridge of flyover groove and prevent the outflow of metal. On the other hand, reducing friction can increase the fluidity of materials, improve the filling performance, ensure the filling of forgings, reduce the forming load and improve the service life of molds. Therefore, the production should try to use better lubrication conditions, and pay attention to the forging die flash groove size control to improve the metal flow resistance. The friction coefficient can be reduced by selecting the right lubricant. Reasonable lubrication can form a protective film between billet and mold, can prevent the stock because of the quantity of heat quickly passed to mould and mould temperature drop of rapid heating, to reduce the forming force and improve die life, and to prevent forging and die chamber adhesion, guarantee the forgings have good surface finish and ensure smooth demoulding forgings. At present, there are a variety of lubricants on the market. When selecting lubricant, the advantages and disadvantages of various lubrication methods and the specific characteristics of mold and blank material should be considered comprehensively, so as to obtain the best lubrication effect, reduce the forming force and extend the life of mold.
3. Mould Material Selection
During forging, the mould works continuously under high temperature environment and undergoes high deformation resistance and thermal stress.Therefore, the forging die manufacturing, must consider the mold stress conditions and temperature conditions, to ensure that the strength, hardness and toughness of the mold to meet the production requirements, choose the mold materials meet the requirements, to avoid the mold material performance can not meet the requirements caused by premature failure of the mold caused by economic losse.
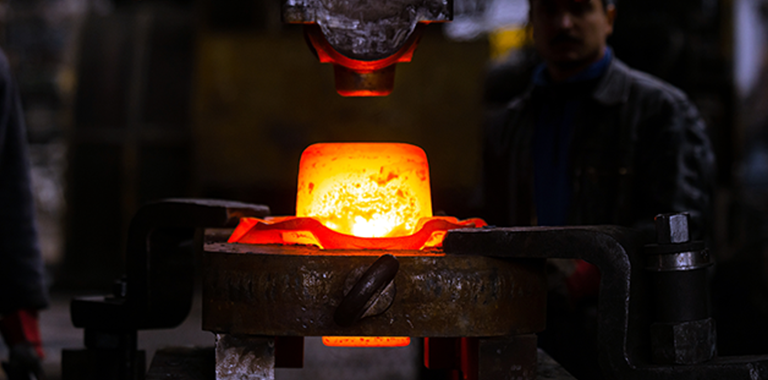
1. Control of Pre-Forging Heating
In hot forging, the metal blank is heated to a certain temperature before forging. Can reduce the strength of the metal limit b sigma, improve its plasticity, and the higher the heating temperature, the greater the b sigma reduction, the required forming force is lower. In order to reduce the forming force and energy consumption, the heating temperature of the metal blank should be raised as far as possible on the premise of avoiding the occurrence of overburning of the metal. As the aluminum forging temperature range is narrow, so we should pay more attention to the control of pre-forging heating.
2. Lubrication During Deformation
In the forging process, the lubrication between the die and the blank is closely related to the forging quality, the forming load and the life of the die. When the lubrication is poor, the friction coefficient increases, the metal material in the mold chamber fluidity is poor. When the lubrication is good, the smaller the friction coefficient, is conducive to the flow of metal materials fill. The influence of friction coefficient on forging is twofold. On the one hand, the increase of friction force can increase the resistance at the bridge of flyover groove and prevent the outflow of metal. On the other hand, reducing friction can increase the fluidity of materials, improve the filling performance, ensure the filling of forgings, reduce the forming load and improve the service life of molds. Therefore, the production should try to use better lubrication conditions, and pay attention to the forging die flash groove size control to improve the metal flow resistance. The friction coefficient can be reduced by selecting the right lubricant. Reasonable lubrication can form a protective film between billet and mold, can prevent the stock because of the quantity of heat quickly passed to mould and mould temperature drop of rapid heating, to reduce the forming force and improve die life, and to prevent forging and die chamber adhesion, guarantee the forgings have good surface finish and ensure smooth demoulding forgings. At present, there are a variety of lubricants on the market. When selecting lubricant, the advantages and disadvantages of various lubrication methods and the specific characteristics of mold and blank material should be considered comprehensively, so as to obtain the best lubrication effect, reduce the forming force and extend the life of mold.
3. Mould Material Selection
During forging, the mould works continuously under high temperature environment and undergoes high deformation resistance and thermal stress.Therefore, the forging die manufacturing, must consider the mold stress conditions and temperature conditions, to ensure that the strength, hardness and toughness of the mold to meet the production requirements, choose the mold materials meet the requirements, to avoid the mold material performance can not meet the requirements caused by premature failure of the mold caused by economic losse.