Drop Forging vs. Casting
When it comes to manufacturing metal parts, there are several methods that can be used. Two of the most popular methods are drop forging and casting. Both methods have their advantages and disadvantages, and which one you choose will depend on the specific requirements of your project. In this article, we will take a closer look at drop forging and casting and compare them in terms of their advantages and disadvantages.
Drop forging is a metalworking process in which a metal part is formed by hammering a heated metal bar into the desired shape. The process is called "drop" forging because the hammer or press drops onto the metal bar to create the shape.
Advantages of Drop Forging
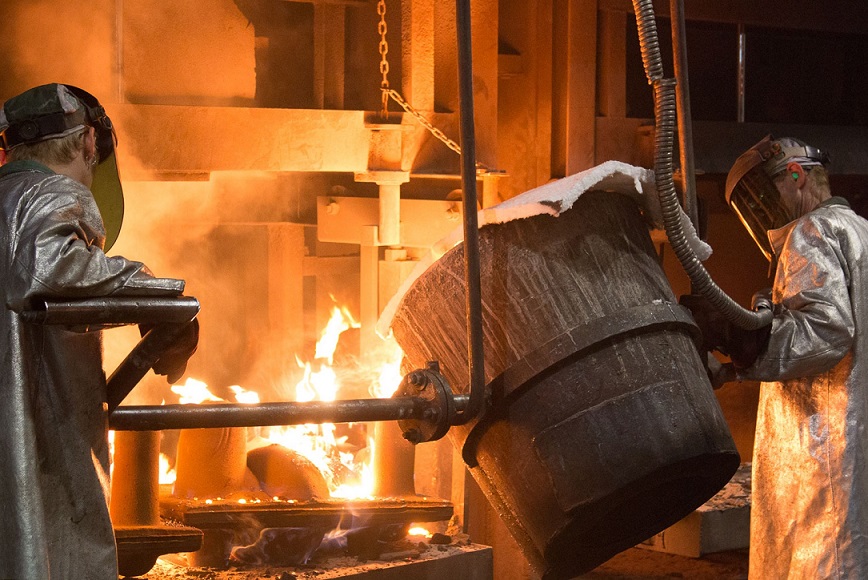
Casting is a manufacturing process in which a liquid material, such as molten metal or plastic, is poured into a mold and allowed to cool and solidify into the desired shape.
Advantages of Casting
When deciding between drop forging and casting, it's important to consider the specific requirements of your project. If you need parts that are strong, precise, and have a good surface finish, drop forging is likely the better choice. If you need parts with greater design flexibility, faster lead times,and are willing to accept some trade-offs in strength and precision, casting may be the better option.
Another factor to consider is the production volume. Drop forging is generally more cost-effective for larger production runs, while casting may be more cost-effective for smaller runs.
It's also worth noting that there are variations of both drop forging and casting that can be used to further tailor the manufacturing process to your specific needs. For example, there are different types of drop forging, such as open die forging and closed die forging, which can be used to produce different types of parts.
Similarly, there are different types of casting, such as sand casting and investment casting, which can be used to produce parts with varying levels of precision and surface finish.
Ultimately, the choice between drop forging and casting will depend on a variety of factors, including the specific requirements of your project, the production volume, and the available resources and expertise. By carefully considering these factors and working with an experienced manufacturing partner, you can ensure that you choose the best method for your needs and achieve the desired results.
Drop Forging
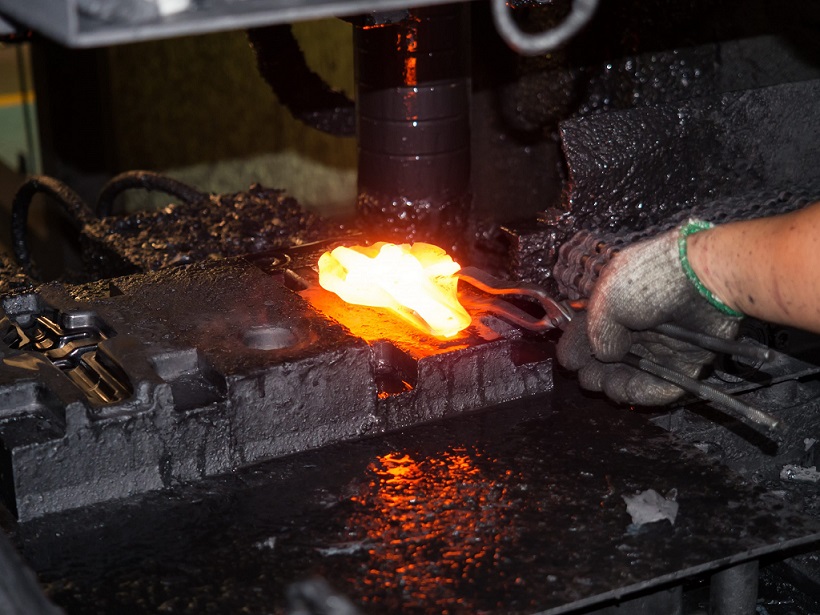
Drop forging is a metalworking process in which a metal part is formed by hammering a heated metal bar into the desired shape. The process is called "drop" forging because the hammer or press drops onto the metal bar to create the shape.
Advantages of Drop Forging
- Stronger Parts: Drop forging produces parts that are stronger than cast parts. This is because the metal is compressed and shaped by the force of the hammer or press, which creates a more uniform grain structure and eliminates any voids or porosity in the metal.
- Better Surface Finish: Drop forging also produces parts with a better surface finish than casting. The process removes any surface defects or blemishes in the metal, resulting in a smooth and polished surface.
- Greater Precision: Drop forging is a highly precise process that allows for tight tolerances and complex shapes. This makes it an ideal choice for parts that require high accuracy and consistency.
- Cost-effective: Although drop forging requires specialized equipment and skilled labor, it can be a cost-effective manufacturing method in the long run. This is because the parts produced through drop forging are stronger and have a longer lifespan than cast parts, reducing the need for frequent replacements.
- Limited Design Flexibility: Drop forging is a process that requires specific shapes and sizes of molds to be used. This limits the design flexibility of the parts that can be produced through drop forging.
- Longer Lead Times: Drop forging requires the production of specialized molds, which can take longer to create than the molds used in casting. This can result in longer lead times for production.
- Higher Initial Costs: The specialized equipment and skilled labor required for drop forging can result in higher initial costs than other manufacturing methods.
Casting
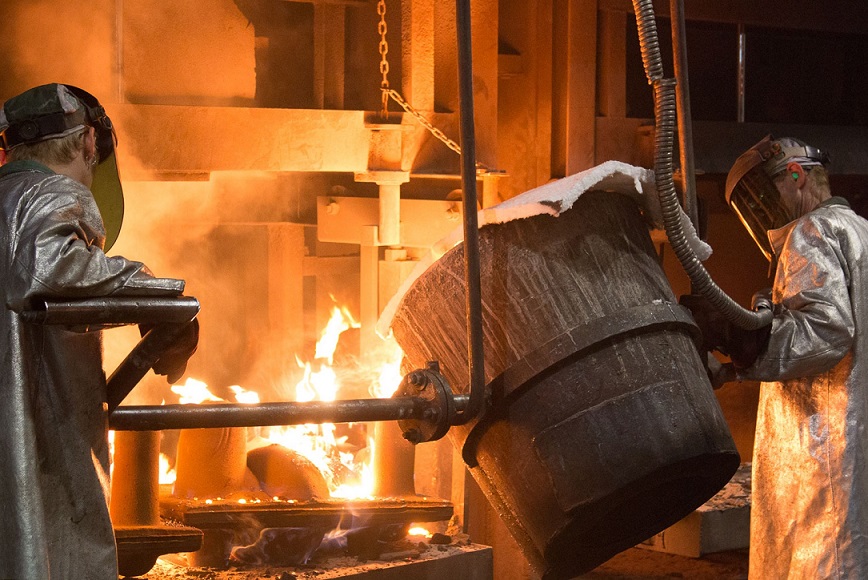
Casting is a manufacturing process in which a liquid material, such as molten metal or plastic, is poured into a mold and allowed to cool and solidify into the desired shape.
Advantages of Casting
- Design Flexibility: Casting offers greater design flexibility than drop forging. The molds used in casting can be made in a variety of shapes and sizes, allowing for a wider range of parts to be produced.
- Lower Initial Costs: Casting requires less specialized equipment and labor than drop forging, making it a more cost-effective manufacturing method for smaller production runs.
- Faster Lead Times: Casting molds can be produced more quickly than drop forging molds, resulting in shorter lead times for production.
- Weaker Parts: Cast parts are generally weaker than drop forged parts. This is because the cooling and solidification process can create voids and porosity in the metal, which can weaken the structure of the part.
- Lower Precision: Casting is a less precise process than drop forging, which can result in parts with looser tolerances and less complex shapes.
- Poorer Surface Finish: Cast parts often have a rougher surface finish than drop forged parts, which can require additional finishing work to achieve the desired appearance.
Drop Forging vs. Casting: Which is Right for Your Project?
When deciding between drop forging and casting, it's important to consider the specific requirements of your project. If you need parts that are strong, precise, and have a good surface finish, drop forging is likely the better choice. If you need parts with greater design flexibility, faster lead times,and are willing to accept some trade-offs in strength and precision, casting may be the better option.
Another factor to consider is the production volume. Drop forging is generally more cost-effective for larger production runs, while casting may be more cost-effective for smaller runs.
It's also worth noting that there are variations of both drop forging and casting that can be used to further tailor the manufacturing process to your specific needs. For example, there are different types of drop forging, such as open die forging and closed die forging, which can be used to produce different types of parts.
Similarly, there are different types of casting, such as sand casting and investment casting, which can be used to produce parts with varying levels of precision and surface finish.
Ultimately, the choice between drop forging and casting will depend on a variety of factors, including the specific requirements of your project, the production volume, and the available resources and expertise. By carefully considering these factors and working with an experienced manufacturing partner, you can ensure that you choose the best method for your needs and achieve the desired results.