Closed Die Forging Company
What is Closed Die Forging?
Closed die forging is also called impression die forging. In closed-dies, solid round bar is heated and placed in a die resembling a mold, which is attached to the anvil. Usually the hammer die is shaped as well. The hammer is then dropped on the workpiece, causing the metal to flow and fill the die cavities. The hammer is generally in contact with the workpiece on the scale of milliseconds. Depending on the size and complexity of the part the hammer may be dropped multiple times in quick succession. Excess metal is squeezed out of the die cavities; this is called flash. The flash cools more rapidly than the rest of the material; this cool metal is stronger than the metal in the die so it helps prevent more flash from forming. This also forces the metal to completely fill the die cavity. After forging the flash is trimmed off.
In commercial closed-die forging, the workpiece is usually moved though a series of cavities in a die to get from an ingot to the final form. The first impression is used to distribute the metal into the rough shape in accordance to the needs of later cavities; this impression is called a edging, fullering, or bending impression. The following cavities are called blocking cavities in which the workpiece is working into a shape that more and more resembles the final product. These stages usually impart the workpiece will generous bends and large fillets. The final shape is forged in a final or finisher impression cavity. If there is only a short run of parts to be done it may be more economical for the die to lack a final impression cavity and rather machine the final features.
Variations of Closed Die Forging
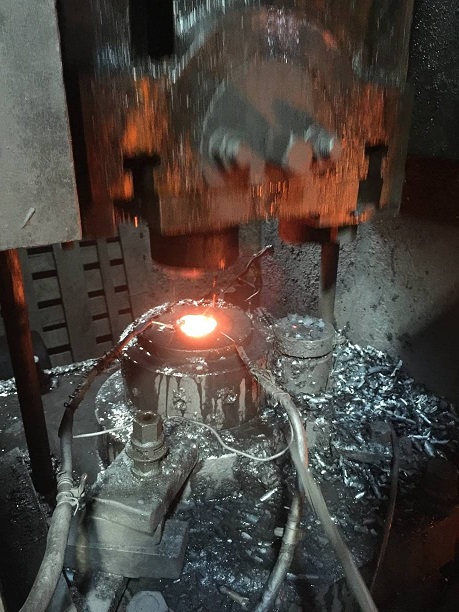
One variation of closed die forging is called flashless forging, or true closed-die forging. In this type of forging the die cavities are completely closed, which keeps the workpiece from forming flash. The major advantage to this process is that less metal is lost to flash. Flash can account for 20 to 45% of the starting material. The disadvantages of this process included: additional cost due to a more complex die design, the need for better lubrication, and better workpiece placement.
There are other variations of part formation that integrate closed die forging. One method incorporates casting a forging preform from liquid metal. The casting this then removed after it's cooled to a solid state, but while still hot. It is then finished in a single cavity die. The flash is trimmed and then quenched to room temperature to harden the part. Another variation follows the same process as outlined above, except the preform is produced by the spraying deposition of metal droplet into shaped collectors (similar to the osprey
process).
Closed die forging has a high initial cost due to the creation of dies and required design work to make working die cavities. However, it has low reoccurring costs for each part, thus forgings become more economical with more volume. This is one of the major reasons forgings are often used in the automotive and tool industry. Another reason forgings are common in these industrial sectors is because forgings generally have about a 20% higher strength to weight ratio compared to cast or machined parts of the same material.
Dies for Closed Die Forging Process
Dies used in closed die forging process are usually made of high-alloy or tool steel. Dies must be impact resistant, wear resistant, maintain strength at high temperatures, and have the ability to withstand cycles of rapid heating and cooling. In order to produce a better, more economical die, the following rules should be followed:
1. The dies should part along a single, flat plane if at all possible, If not the parting plan should follow the contour of the part.
2. The parting surface should be a a plane through the center of the forging and not near an upper or lower edge.
3. Adequate draft should be provided; a good guideline is at least 3° for aluminum and 5° to 7° for steel.
4. Generous fillets and radii should be used.
5. Ribs should be low and wide.
6. The various sections should be balanced to avoid extreme difference in metal flow.
7. Full advantage should be taken of fiver flow lines.
8. Dimensional tolerances should not be closer than necessary.
The dimensional tolerances of a steel part produced using the impression-die forging method are outlined in the table below. It should be noted that the dimensions across the paring plane are affected by the closure of the dies, and are therefore dependent die wear and the thickness of the final flash. Dimensions that are completely contained within a single die segment or half can be maintained at a significantly greater level of accuracy.
A lubricant is always used when forging to reduce friction and wear. It is also used to as a thermal barrier to restrict heat transfer from the workpiece to the die. Finally the lubricant acts as a parting compound to prevent the part from sticking in one of the dies.
Closed Die Forging Company-CFS Forge
CFS Forge, one of the largest drop forging companies in China, devotes itself to supplying high quality closed die forgings to our customers from American and Eourpean companies. At the beginning, CFS' closed die forging capability was only limited to steel, but now we are able to supply closed die forgings in steel, aluminum and copper, which makes us to supply more options to our customers.
Why Closed Die Forging from CFS Company?
- CFS' closed die forging process offers some distinct advantages over many forms of casting or open die forging from a manufacturing standpoint.
- Our closed die forging method usually offers a more cost-effective solution than open-die forging for the fulfillment of high volume production runs. This process can generate many small parts quickly.
- Our closed die forging company can create shapes using virtually any type of commercial metal. For example, we can use closed die forging to create parts made from steel, aluminum or brass alloys.
- In our closed die forging company, our custom service supplies parts with better surface finishes than many other forging or casting processes. The parts generated through this process may require only minimal finishing.
- CFS Forge can utilize the process of closed die forging to produce both symmetrical and non-symmetrical metal parts. With the capability to reproduce almost any size and shape of part, this flexible forging process holds widespread appeal in modern manufacturing environments!
- Compared to most forms of forging, the process of closed die forging sometimes offers a way to create metal parts displaying superior mechanical properties. Under rigorously controlled manufacturing conditions, the internal grain structure of the metal components contributes to increased strength and tightness.
- With closed die forging, parts from CFS company do not require extensive machining afterwards. We will just need to trim away any flash. Or, the process of custom closed die forging may allow the generation of blind cores or nearly complete shapes requiring only the most minimal machining and finishing.
- The green manufacturing of closed die forging in CFS company holds some practical daily maintenance advantages. Maintaining a tidy, clean work area typically requires less complicated clean up procedures than casting manufacturing locations demand.