Case Study on Closed Die Forging for Automotive Parts
Closed die forging is generally only applied in automotive application, such as automotive gearboxes, housings, flanges, etc. Closed die forging process can greatly improve the material utilization rate and lengthen the life of automotive parts for its good strength. At the same time, it reduces the production cost, thus, it is an ideal target for automotive parts production.

Closed Die Forging Process
The excircle drafting angle of forging drawing of the closed forging process is 5°, the upper filling edge is permitted to be less than R≤3mm, the burr ≤1mm and the forging weight to be 5.55kg.
The most important part of the closed die forging process is the design of pre-forging die. The pre-forging step mainly plays the role of pre-forming and dosing. In the light of previous experience, with forge software simulation, it is found that the burrs on both sides of the forging are higher when the forging is fully filled. The reasonable design of pre-forging die can ensure that the final forging is fully filled without burrs. The shape of the non-rotational flange is complex and cannot be designed according to previous experience. For the purpose of obtaining closed die forged automotive parts, the forming process must be analyzed and the die must be scientifically and rationally designed. The closed die forging process is formulated as follows: heating → upsetting → pre-forging → final forging → punching → heat treatment → surface cleaning, and the design process of pre-forging die is described in detail.
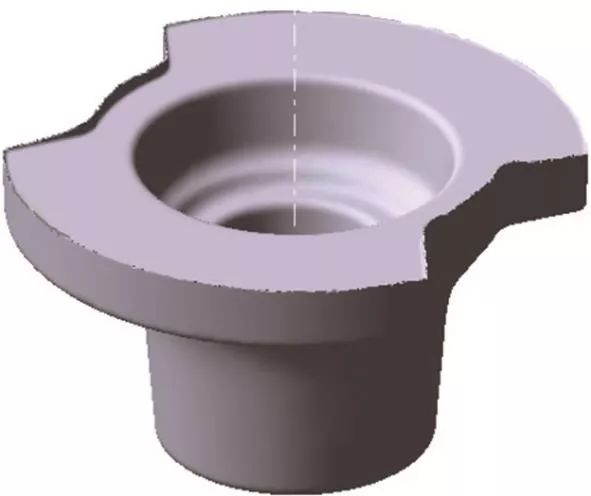
The difficulty in pre-forging die design is to make the metal flow to the fan-shaped parts on both sides and to store enough raw materials to make the final forging process fully filled without burrs. In the forging process, the narrowest area of the forging is the first to be filled. The thickness of the forging is 22mm, so the side thickness of the pre-forging is designed to be 30mm, which can effectively avoid the burr in the forming process. The sharp angle corner on both sides of the forging sector is the most difficult to fill. In order to make the metal flow to the sharp corner, a 7mm resistance wall is designed on the fan-shaped edge of the pre-forging. The shape of the pre-forged hot forging is finally determined by using Forge software to simulate and optimize the design.
The upsetting process is free upsetting. The key point of the design is that the blank rod part can be placed in the pre-forged model cavity after upsetting, and the final size of upsetting is 120mm. The forging process is performed on the 2500t forging press and a simple die punching process was adopted. With the 400t punching machine, the blanking specification is φ80mm×157mm, the material utilization rate is 90%, the height dimension of the sealing material is designed to be 15mm, and the unilateral clearance is designed to be 0.5mm. In this structure, the upper and lower die rings are bolted, which is convenient for die disassembly and assembly. It saves assembly time, only the upper and lower dies need to be replaced when other types of automotive parts need to be changed and the die cost is reduced by 25%.
Summary
Above introduces the closed die forging process of automotive parts and comes up with new ideas in many designs and it was applied in many fields. This forging process can be widely used in other applications as well. CFS Forge can make closed die forgings in various metals, including steel, aluminum and brass. Any inquiry on closed die forging, pls contact us for a free quote right now!