Aluminum Forging vs. Aluminum Casting
Aluminum Forging
Forging is a manufacturing process where metal is pressed under great pressure to produce high-strength parts. Aluminum Forging is ideal for applications where performance and safety are critical but a lighter-weight metal is needed for speed or energy efficiency. Common aluminum forging alloys include: 6061, 6063, 7075, etc.
Aluminum Casting
Aluminum casting is a simple, inexpensive and versatile way of forming aluminum into a wide array of products. There are several methods of aluminum castings, including die casting, gravity casting and sand casting. Common aluminum casting alloys include: A356, A380, etc.
Aluminum Forging vs. Aluminum Casting
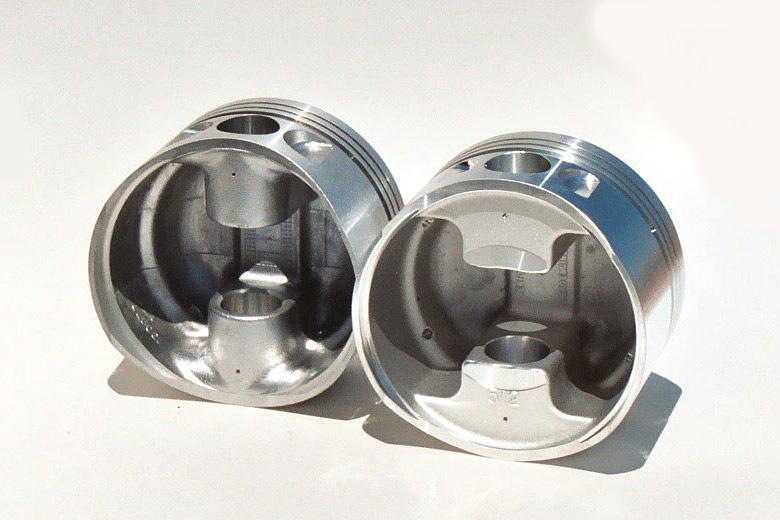
Since aluminum forging and casting are the two kinds of different manufacturing processes. Then, what are the main differences between aluminum forging and aluminum casting? Which is better? Below are the main aspects:
Strength
When treated with heat, aluminium forgings show certain mechanical properties that make their strength to weight ratio far superior than that of aluminum castings. Besides, forging is porosity-free. Also, heat treatment can help to improve the strength of aluminum forgings. This greater strength of aluminum forging can obtain better working preformance and longer serving life.
Cost
The tooling cost of aluminum forgings are generally cheaper than that of aluminum casting. When there are numerous fabrications options that are feasible for certain applications, cost becomes a major deciding factor. The production rate of aluminum forging is also higher than that of casting. In highly stressed applications, there are many forgings used as against castings as they are more affordable.
Lead Time
The standard lead time of aluminum forging can be controlled with 5-7 weeks. Today, toolmakers are introducing cost-effective technology to reduce the time frame of their production. Less time means less spend. To lessen the lead time, forging production centres usually have self-contained spaces. This in return provides them with higher regulation & control in the creation as well as revisions on a timely basis.
Surface Finish
A variety of surface treatment can be operated after aluminum forging. The surface finish of casting is not very visually appealing or smooth. However, aluminium forging makes it easy for the creation of smooth surfaces or sharper serrations. Some aluminum forging alloys, like 6061, have the most sought-after anti-corrosion traits sans any surface finishes.
Flexibility
Although not all shapes of aluminum components are forged, there are certain exceptions. Produced out of a die tooling designer, forging can give out surprisingly different shapes. The use of 3D modelling and drawings has also vastly increased the flexibility of the models in the early design phases. Unlike casting, where the physical size of the component may restrict flexibility in design, aluminum forged components are flexible when it comes to new design suggestions from clients.
Looking for aluminium forging manufacturers for your business? CFS Drop Forging is a leading manufacturer of closed die forged components in high strength aluminium alloys, and can supply custom service for your source of aluminum hot forging including machining.