Aluminum Forging: Perfect Manufacturing Process for Companies
Drop forging can generate a part that's more powerful than an equal investment casting or even machined part. Since the metal is formed during the irrigation process, its inner grain feel deforms to adhere to the overall form of this part. Because of this, the texture variation is constant through the component, giving rise to some bit with enhanced power characteristics. Additionally, drop forgings may attain a lower overall cost than simply casting or manufacture. Considering all of the expenses which are incurred at a product's life cycle from procurement to direct time to rework, and factoring in the prices of waste, and downtime along with other high-quality factors, the long-term advantages of both drop forgings can outweigh the short-term price savings which castings or fabrications might provide.
A lot of alloys are involved in the drop forging process, such as steel, aluminum or copper. The selection of the forging process is based on the sizes and type of the part involved. So, metals requiring precipitation hardening are always hot forged given to their properties.
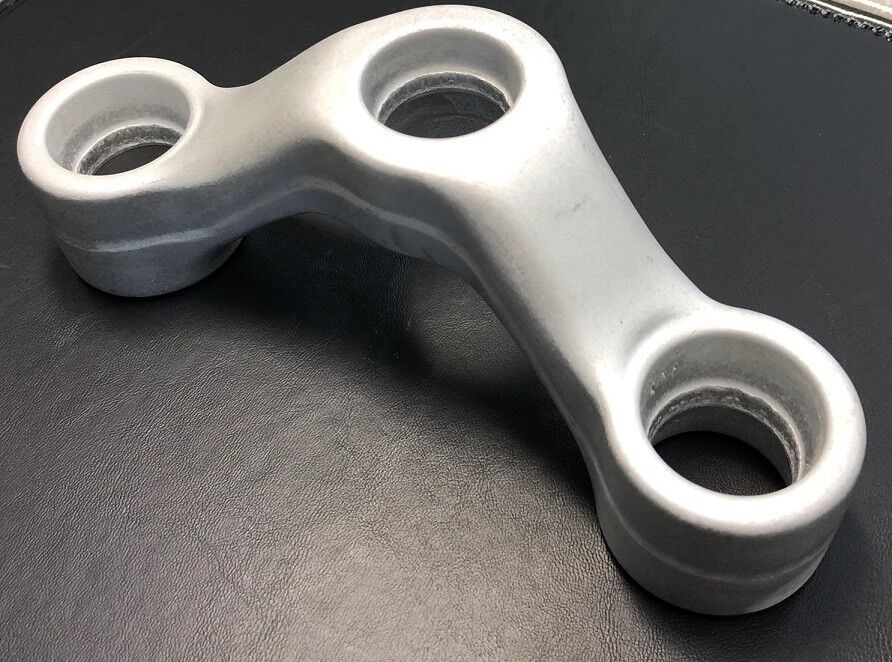
Aluminum forging is the common type that is easily accessible for its light weight and good strength. They are available in all shapes and sizes. Aluminium forging is not only easy but also quicker to establish. The net output is also light in weight and, hence, easy to carry around or transport compared to its rival counterparts. The strength of the produce through aluminium forging can also be controlled as per the maker's desire. They can be made subtle or strong depending on the need or end usage. Forged aluminum components have a direct strength to weight ratio so the manufacturer knows how much forging needs to be involved in order to gain the desired output. The best part about them is that they last for very long as they are rust-free and have high resistance against environmental changes, chemicals and toxic materials.
A lot of properties possessed by forged aluminum components make them favorite amongst aluminum forging companies. Compared to other metals, aluminium conducts heat effortlessly which other metals would not be able to do at the same given price. This makes it economic for users to opine for it. When it comes to power consumption, again, forged aluminum components are given a higher preference compared to other metals since they conduct electricity very well and are more efficient.
Metals can be molded into a variety of designs and can be put to utility at a number of places. These components are also availed at a lower rate and are economic in price and their usability is much more compared to other forged alloys and metals. This feature gives them an edge over the other existing components in the market. Hence, they applied for a number of purposes, fields and in industries involved in variety of productions. Their versatile features make aluminium forging one of the most extensively used manufacturing technique in the industry.
Related Article:
A lot of alloys are involved in the drop forging process, such as steel, aluminum or copper. The selection of the forging process is based on the sizes and type of the part involved. So, metals requiring precipitation hardening are always hot forged given to their properties.
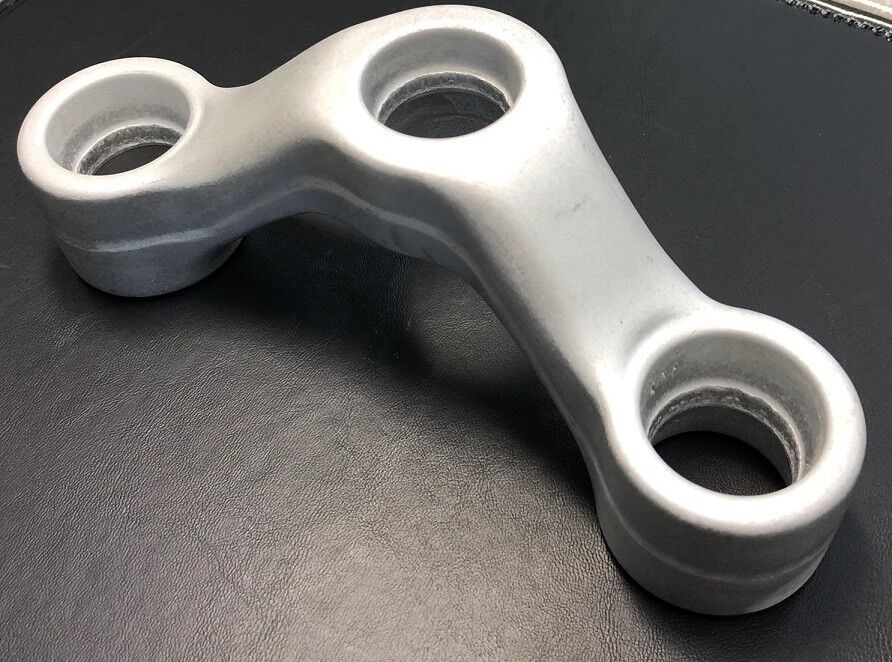
Aluminum forging is the common type that is easily accessible for its light weight and good strength. They are available in all shapes and sizes. Aluminium forging is not only easy but also quicker to establish. The net output is also light in weight and, hence, easy to carry around or transport compared to its rival counterparts. The strength of the produce through aluminium forging can also be controlled as per the maker's desire. They can be made subtle or strong depending on the need or end usage. Forged aluminum components have a direct strength to weight ratio so the manufacturer knows how much forging needs to be involved in order to gain the desired output. The best part about them is that they last for very long as they are rust-free and have high resistance against environmental changes, chemicals and toxic materials.
A lot of properties possessed by forged aluminum components make them favorite amongst aluminum forging companies. Compared to other metals, aluminium conducts heat effortlessly which other metals would not be able to do at the same given price. This makes it economic for users to opine for it. When it comes to power consumption, again, forged aluminum components are given a higher preference compared to other metals since they conduct electricity very well and are more efficient.
Metals can be molded into a variety of designs and can be put to utility at a number of places. These components are also availed at a lower rate and are economic in price and their usability is much more compared to other forged alloys and metals. This feature gives them an edge over the other existing components in the market. Hence, they applied for a number of purposes, fields and in industries involved in variety of productions. Their versatile features make aluminium forging one of the most extensively used manufacturing technique in the industry.
Related Article: