Aluminum Forging For Motorcycle Brake Caliper
Application of Motorcycle Brake Caliper
As the "brake pump" inside the brake system, the motorcycle brake caliper mainly receives the hydraulic pressure transmitted by the brake master pump through the brake oil pipe, then the hydraulic pressure was applied to the piston inside the caliper. The piston then pushes the brake pad and makes it combined with the brake disc, and the vehicle is decelerated by the friction between them, and the kinetic energy of the vehicle is converted into frictional heat and dissipated in the air.
Aluminum Forging for Motorcycle Brake Caliper
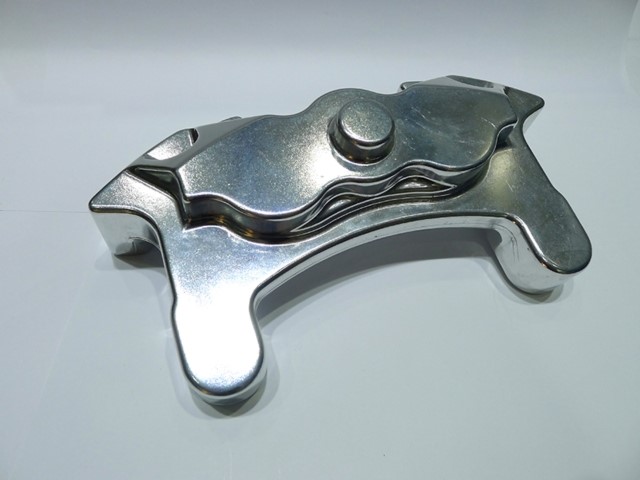
Since the brakes are frequently used during the motorcycle moving, the motorcycle brake calipers often receive the hydraulic pressure transmitted by the brake master pump as well as the reaction force of the brake pads to the brake calipers. Meanwhile, the calipers will also be repeatedly affected by the high temperature generated by the brake pads’ frictional heat. The common motorcycle brake calipers are generally made of cast aluminum alloy. Although the high temperature and pressure during braking will not cause the motorcycle brake calipers to be destroyed due to the metal fatigue strength, there will be some deformation, which will lead to a decrease in braking performance and a series of problems, such as brake imbalance. Therefore, the motorcycle brake caliper will be more durable with the aluminum forging process. Its advantages include: high strength forging process, excellent performance, lighter weight, higher temperature resistance and wide applicability. But the calipers can also be made by casting with the advantages of low price and the mature process, and it can meet the daily use, while its performance is common and its quality is heavier and was widely used in the original production car.
Aluminum Forging vs. Aluminum Casting for Motorcycle Brake Caliper
Usually, the motorcycle brake caliper is made by the process of casting or forging. In short, the mechanical strength of the motorcycle brake caliper with the aluminum forging process is higher than that of the aluminum casting, but the price of the casting caliper is relatively low, which has a direct relationship with the manufacturing cost.
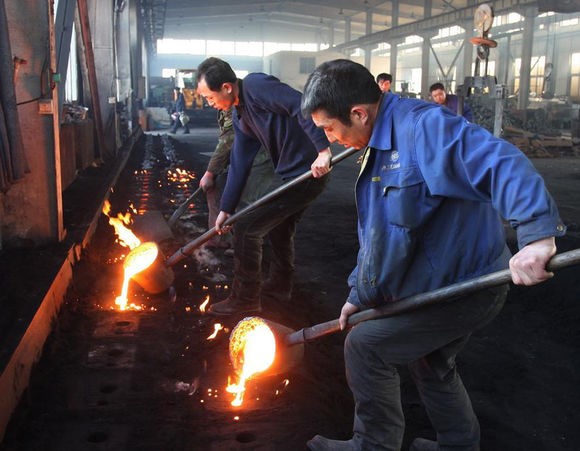
Assisted with the casting mold, the casting motorcycle brake caliper is formed after the melted aluminum ingot is poured into the mold and to be solidified and finally the metal burr, joint flash and somethings like that are removed, then the production of a motorcycle brake caliper body is completed.
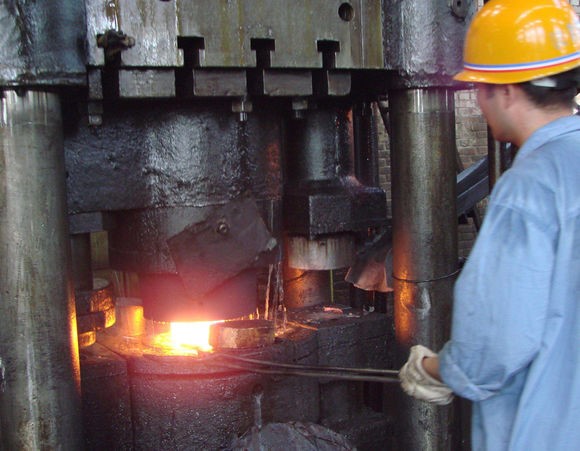
As raw materials, 6061 aluminum alloy and 7075 aluminum alloy are used in the forging of motorcycle brake calipers. The basic shape of the brake caliper is forged by high pressure and then CNC machined. This kind of material structure is more compact and the heat dissipation performance and material rigidity are better than the casting materials. Among them, 7075 aluminum alloy is basically the most high-end motorcycle brake caliper material on the market and is generally used in track products.
In summary, aluminum forging for motorcycle brake caliper has the characteristics of finer surface, higher surface finish and smoother chamfer. With the excellent performance, aluminum forged motorcycle brake calipers can be mass produced for different vehicles. In Europe and the United States, the modified motorcycle brake caliper is basically based on aluminum forging.
Surface Anodization Treatment
The surface treatment of modified motorcycle brake caliper is mostly based on conventional anodization, and the high-end performance motorcycle brake calipers use hard oxidation. Then let's talk about the differences between these two types of anodization treatments.
Conventional Anodization
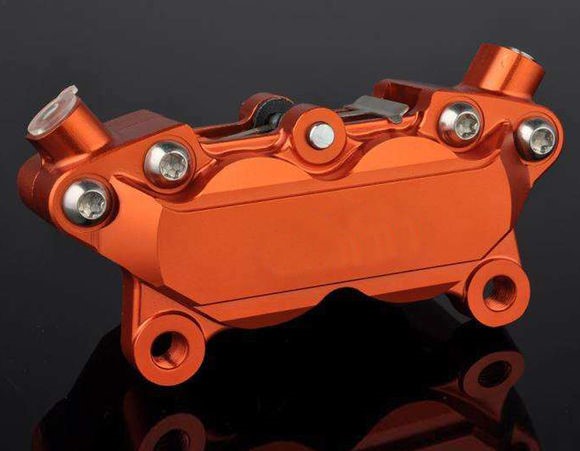
Conventional anodization refers to the process in which aluminum and its alloys form an oxide film on an aluminum product due to an impressed current under the conditions of corresponding electrolyte and specific process. The advantages of conventional anodization include the bright color, the low price, anti-corrosion function as well as the high cost performance. The disadvantage is that its hardness is relatively low, the treatment layer is very thin, which is easy to scratch (the scratch is appeared only with a key being gently crossed) and its protection will be lost after the scratch.
Hard Anodization
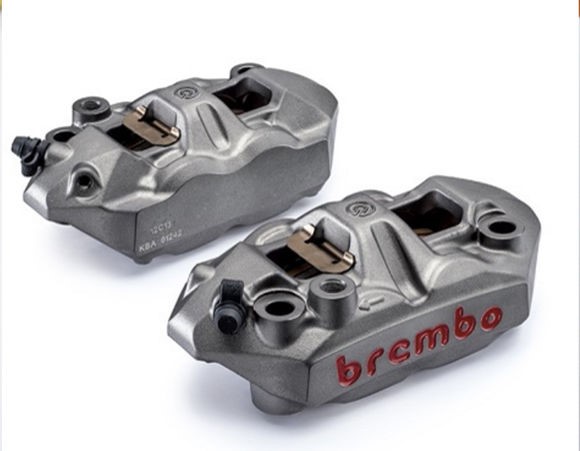
As it is known to all, there is no conventional anodization in BREMBO's motorcycle brake caliper products and alternatively with a hard anodization surface treatment. The hard anodization is similar to conventional anode in principle, but there are differences in regard to the raw materials and processing methods, which make its surface wear resistance is greatly improved. The surface hardness can reach to HV500 and the thickness is 25-250um after the hard oxidation of aluminum alloy. With the strong adhesion, 50% of the formed oxide film penetrates into the aluminum alloy while 50% adheres to the surface of the aluminum alloy.
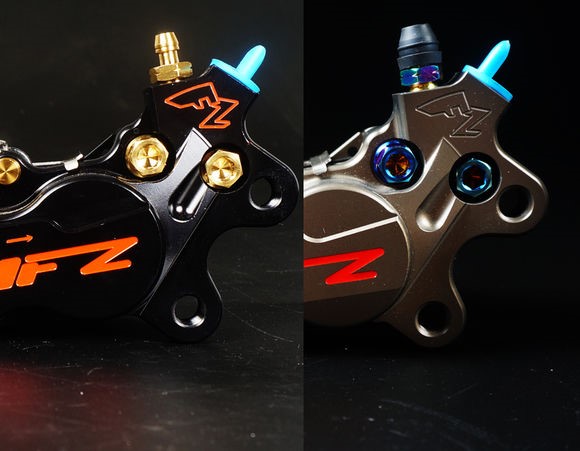
In the mainstream process, hard anodization has the best wear resistance and is widely used in military and other fields. It is the most suitable surface treatment process for high-end functional brake calipers. Its shortcoming is that the price is higher, the color is not bright enough and generally there are only black, khaki, gray etc in colour.
Related Article: