Advantages of Forging
Forging is a manufacturing process by which metal is pressed under great pressure into high strength desired parts. The process is normally (but not always) performed hot by preheating the metal to a desired temperature before it is worked. It’s important to note that the forging process is entirely different from the casting process (forging vs casting), as metal used to make forged parts is never melted and poured as operated in the casting process. Forging refines the grain structure and improves the physical properties of the metal, so that the grain flow can be oriented in the direction of principal stresses encountered in actual use. Physical properties such as strength, ductility, and toughness are much better in a forging than in the base metal.
Below are the detailed description of forging advantages:
1) Forging can refine the grain structure of products. Forging is superior to casting or machining bar stock because the metal’s natural grain flow is made to conform to the shape of the product. Castings have an isotropic grain structure and, for a given part, may be as strong in compression loads, but standard and custom forgings are superior in tensile and shear loads due to the utilization of the grain flow. The structural reliability of forgings allows designers to trust the material to adhere to the safety factors of the design. It also can provide more uniform response to heat treatment and machining operations.
2) Forging process can create parts that are stronger than those manufactured by any other metalworking process. This is why forgings are almost always used when reliability and human safety are critical.
3) Forgings can be nearly any shape, which reduces the need for joining multiple pieces. Reducing the joint can improve the overall strength of the unit as the forging does not need to be welded or otherwise fastened together.
4) Forging can be used to make parts for all industries. Products manufactured by forging in modern industry include critical aircraft parts such as landing gear, shafts for jet engines and turbines, structural components for transportation equipment such as automobiles and railroads, crankshafts, levers, gears, connecting rods, hand tools such as chisels, rivets, screws, and bolts to name a few.
5) The manufacture of forging die and the other high costs of setting up an operation make the production of small quantities of forged parts expensive on a price per unit basis. Once set up, however, operation costs for forging manufacture can be relatively low, and many parts of the process may be automated. These factors make manufacturing large quantities of metal forgings economically beneficial.
What Does CFS Forge Offer?
CFS Forge is the premier closed die forging provider. With annual output 10,000t, we have totally six production lines to ensure timely delivery. In our forging factory, we have forging equipments from 300t to 2,500t, so that we can supply both small and medium components at your service. Besides, we can also offer below services:
1) We have our own tool & die shop, forging shop, and machining shop. So we can supply products in different status. No matter whatever products you need, we have the ability to make forging dies, forging blanks, and machined forgings. Compared to other forging compaines, we also have experience of delivering forging dies only according to the prints or samples.
2) Redesign service--Once you feel that your current design is too costly, or the working performance is not very good. Come to our company, our engineer can help you to redesign the part combing our forging experience and your application. To improvide our customer service, our redesign service is free of cost.
3) Convert casting into forging - It is common that defects are always produced in casting. So when you would like to change the metal casting way of your products into forging, Fly Forge will be your wise choice for this job. We will revaluate your current design and give you a new forging solution for reference.
4) We offer not only forging parts--We have our own casting foundry. Of course, we can also help to source other products, such as stampings, metal fabrications, etc. This enables us to become a comprehensive service company.
Below are the detailed description of forging advantages:
1) Forging can refine the grain structure of products. Forging is superior to casting or machining bar stock because the metal’s natural grain flow is made to conform to the shape of the product. Castings have an isotropic grain structure and, for a given part, may be as strong in compression loads, but standard and custom forgings are superior in tensile and shear loads due to the utilization of the grain flow. The structural reliability of forgings allows designers to trust the material to adhere to the safety factors of the design. It also can provide more uniform response to heat treatment and machining operations.
Grain Flow Comparision | ||
Forging |
Casting | Machining |
![]() |
![]() |
![]() |
Grain flow is oriented to improve ductility,
toughness, and increase fatigue resistance |
Typically do not have a desired grain structure |
Uni-directional grain flow has been cut when
changing contour, exposing grain ends. This renders the material more liable to
fatigue and more sensitive to stress corrosion cracking |
2) Forging process can create parts that are stronger than those manufactured by any other metalworking process. This is why forgings are almost always used when reliability and human safety are critical.
3) Forgings can be nearly any shape, which reduces the need for joining multiple pieces. Reducing the joint can improve the overall strength of the unit as the forging does not need to be welded or otherwise fastened together.
4) Forging can be used to make parts for all industries. Products manufactured by forging in modern industry include critical aircraft parts such as landing gear, shafts for jet engines and turbines, structural components for transportation equipment such as automobiles and railroads, crankshafts, levers, gears, connecting rods, hand tools such as chisels, rivets, screws, and bolts to name a few.
5) The manufacture of forging die and the other high costs of setting up an operation make the production of small quantities of forged parts expensive on a price per unit basis. Once set up, however, operation costs for forging manufacture can be relatively low, and many parts of the process may be automated. These factors make manufacturing large quantities of metal forgings economically beneficial.
What Does CFS Forge Offer?
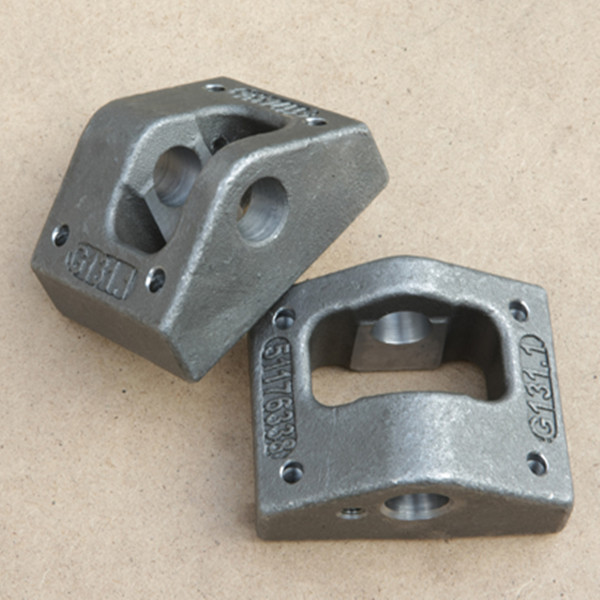
1) We have our own tool & die shop, forging shop, and machining shop. So we can supply products in different status. No matter whatever products you need, we have the ability to make forging dies, forging blanks, and machined forgings. Compared to other forging compaines, we also have experience of delivering forging dies only according to the prints or samples.
2) Redesign service--Once you feel that your current design is too costly, or the working performance is not very good. Come to our company, our engineer can help you to redesign the part combing our forging experience and your application. To improvide our customer service, our redesign service is free of cost.
3) Convert casting into forging - It is common that defects are always produced in casting. So when you would like to change the metal casting way of your products into forging, Fly Forge will be your wise choice for this job. We will revaluate your current design and give you a new forging solution for reference.
4) We offer not only forging parts--We have our own casting foundry. Of course, we can also help to source other products, such as stampings, metal fabrications, etc. This enables us to become a comprehensive service company.