Company Profile
CFS Machinery CO.,LTD, established in year of 2001, is a leading professional closed die drop forging manufacturer & exporter, located in Ningbo, China. Our drop forging company specializes in producing all kinds of
steel forgings,
aluminum forgings and
copper forgings involved in mining machinery, construction machinery, automotive components, oil & gas industry, etc. We could serve drop forged components in
closed die forging process ranging from 0.05kg-100kgs.
In our drop forging factory, there are totally 250 staffs working here, with 218 workers, 6 engineers, 8 QC men, 10 sellers and 8 administrative staff. We have advanced production and testing equipments. Our production equipments consist of moulding equipments, forging equipments and machining equipments. Besides, we also have our own heat treatment workshop, including normalization, quenching, tempering & hardening, etc. Under the hard-working of all staff, we could reach an annual output 10,000t of drop forgings.
At present, all of our drop forgings are mainly exported to companies from America, UK, Canada, Australia, etc. Our advanced drop forging process, complete production & testing equipments and experienced technical team, all help CFS Forge supplying qualified drop forged products and good service. Currently, we are issued with TS16949, API & ISO9001:2008 certifications, lots of customers are turning to our company to produce drop forgings like auto parts, oilfield pipe fittings, foundation drill bits, and so on.
Today, CFS company continues to enlarge our company's scale to creat a world-class
drop forging supplier. We are now also developing robots as the workforce to save labour costs and improve production efficiency.
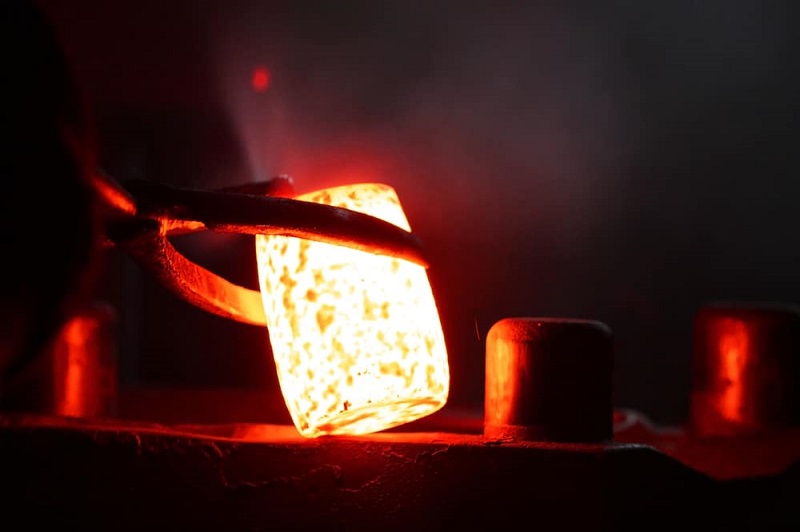
Drop Forging is a metalworking process that deforms metal by applying pressure, usually at high temperatures. So, temperature control is a necessary step in drop forging production, and there is a strict temperature control requirement on each type of forged metal. For instance, steel forging usually requires to heat billets to 950°C and 1250°C, while aluminum forging and brass forging have lower heating temperature requirement. Aluminum forging can be performed at temperatures between 350°C and 500°C, and the ideal forging temperatures of brass forging range from 600°C to 950°C.
CFS Forge has been in drop forging industry for over 25 years, we usually control the temperature for forging production by induction heating furnace. This heating equipment can provide rapid and uniform heating, allowing precise control over the temperature and heating rates of the forging billets, thus improving consistency.
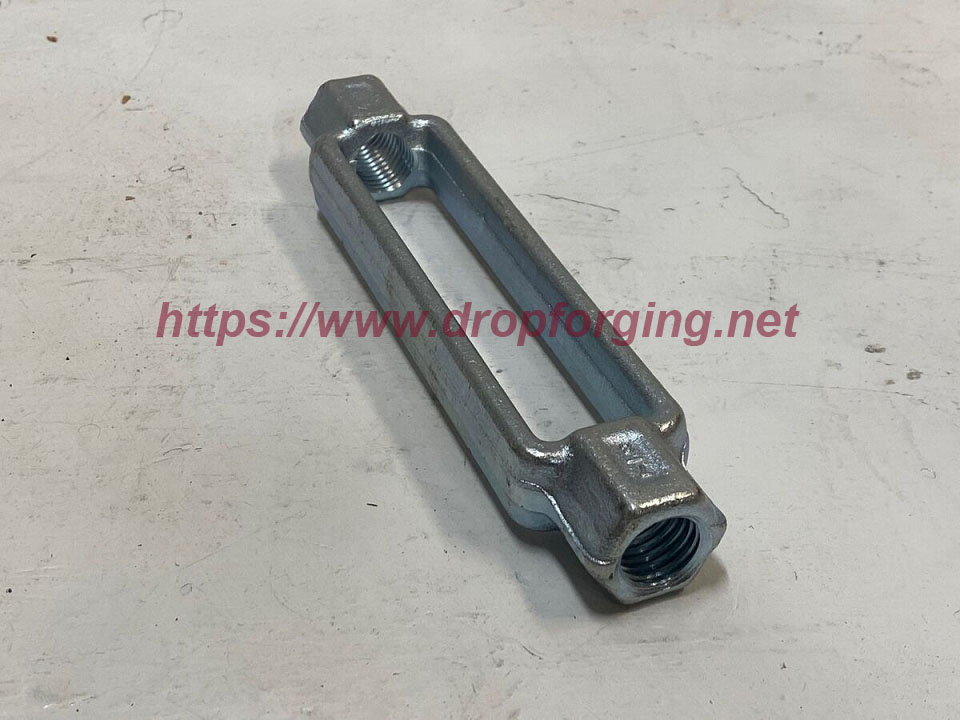
Drop forging is an excellent process for making high-strength components like turnbuckle bodies. Known for its ability to enhance metal properties, drop forging ensures the strength, load-carrying capacity, and precision structural hardware needs.
CFS Forge is the top leading China drop forging company, we are very familar with the manufacturing process of drop forged turnbuckle bodies. In this article, we would like to share all that you might want to know about drop forging technique and its process to create turnbuckle bodies.
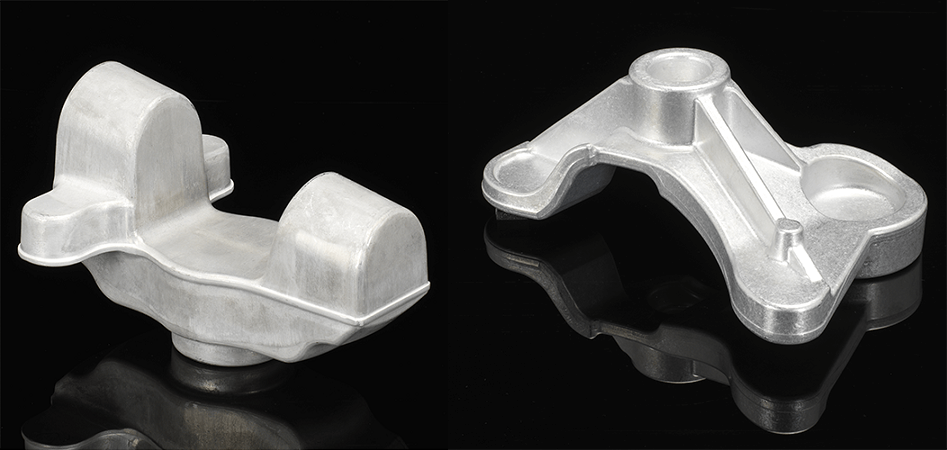
With the development of forging technique, aluminum alloys are more and more popular in forging production due to their great strength, light weight, and corrosion resistance. CFS Forge is the top China aluminum forging company
, specializing producing custom forged aluminum parts in various alloys, such as 2014, 6061, 6063, 6082, and 7075 alloys. Among these alloys, each has its special features and advantages. In this article, we would like to compare 6082 and 7075 aluminum alloys for forging, which can help our customers to choose a proper alloy for their project.
Both 6082 and 7075 aluminum alloys offer unique advantages for drop forging applications. 6082 excels in corrosion resistance, weldability, and cost-effectiveness, making it ideal for structural components and environments where these factors are critical. On the other hand, 7075 provides unmatched strength and hardness, suitable for high-stress applications in the aerospace and defense industries. Understanding the specific requirements of your application is essential in making the right choice. CFS team can recommend the best suitable aluminum alloy for your forged item.
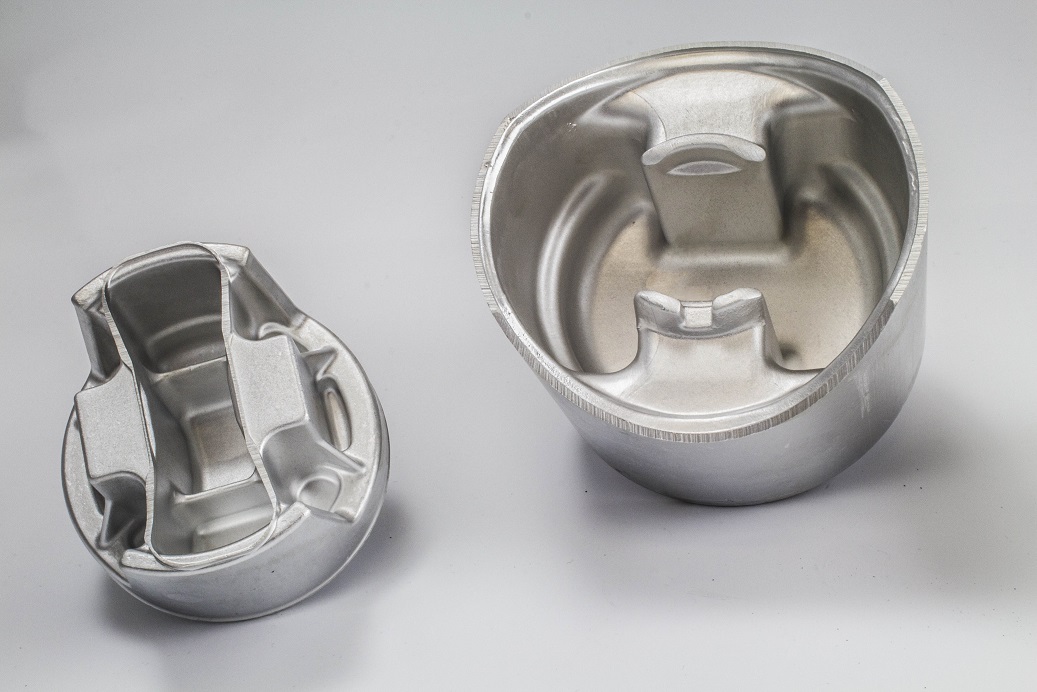
Motorcycle pistons is an important component for generating power in vehicles and work under high temperature and high pressure conditions. It is also a critical component in maintaining normal workflow. CFS Forge is the top leading forging manufacturer in China, we have rich experience in forging aluminum pistons for motorcycles. So, we are very familar with the whole manufacturing process of forging aluminum motorcycle pistions.
Are you looking for high-performance forged aluminum pistons for your motorcycle? CFS Forge is your reliable manufacturer for custom forging solutions that meet the highest standards of quality and durability. Would like to know how we can help your project? Contact us today and send us your inquiry for an instant quote now!
For a riding vehicle with two wheels, the choice of material play a vital role on the performance and durability of motorcycles. Due to the balance betwwen lightweight and strength, forged aluminum has been a preferred material to produce motorcycle parts. As the leading aluminum forging company in China, CFS Forge has develpped and produced lots of forged aluminum motorcycle parts for many motorcycle parts dealers or motorcycle manufacturers. Based on our rich experience in aluminum forging of motorcycle parts, we will discuss the advantages of forged aluminum, some typical forged aluminum motorcycle parts, and why choose our company as your parnter.CFS Forge can customize your special designed forged aluminum motorcycle parts with precise dimensions and good surface finish. Besides forging, we can also provide precision machining and surface anodizing services for finished motorcycle parts. Our strict quality control procedure enables us to deliver high quality products and reasonable prices. If you are looking for a good forging company for your motorcycle parts, pls contact us to request a free quote first!
When towing trailers or caravans, safety and reliability is very important. To ensure a secure and stable connection, the towball is designed as a critical components which connects the vehicle to a trailer or caravan. Forged steel is preferred to produce towballs, offering exceptional strength and longevity.
CFS Forge is a professional forging manufacturer, offering top-quality forged steel towballs designed for safety, reliability, and longevity. With advanced forging equipments and strict quality control, CFS Forge is your trusted partner for all your towball needs. Whether you're towing a trailer or caravan, we can customize exactly to meet your specifications . Contact us today to learn more about capabilities and request a free quote shortly.
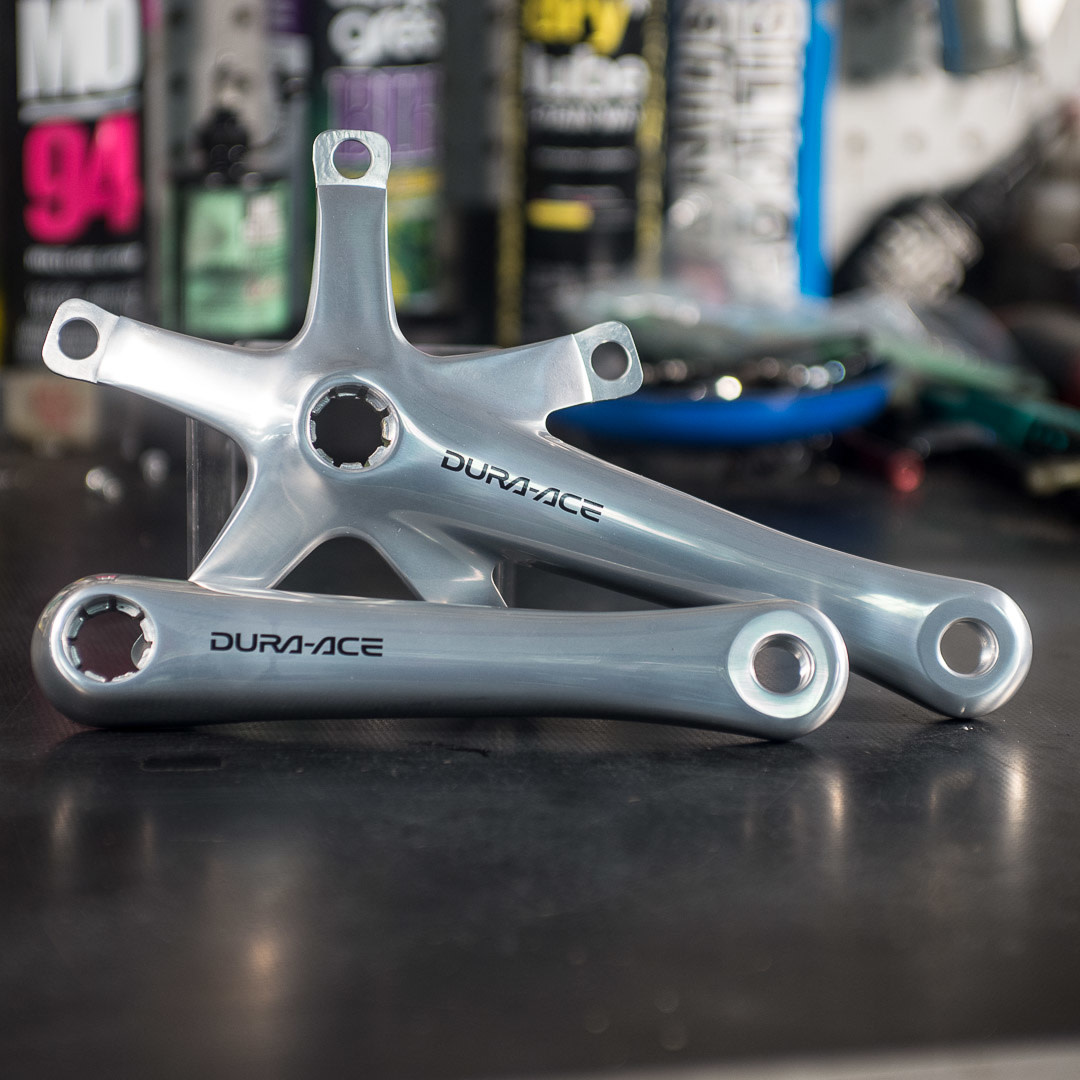
The crank arm is a crucial component of a bicycle's drivetrain system, responsible for transferring the cyclist's leg power into the chain, thus propelling the bicycle forward. Essentially, crank arms are levers connecting the pedals to the bottom bracket spindle, forming a vital connection between the rider and the bike's drivetrain.The choice of manufacturing method plays a significant role in the performance, durability, and weight of a crank arm. Forged aluminum is preferred for crank arms because of its superior structural integrity and lightweight characteristics. Aluminum forging creates parts that are stronger and more reliable than those produced by other manufacturing methods like casting or machining.Forged aluminum crank arms offer a superb stiffness-to-weight ratio, which is a critical parameter for efficient power transfer. They can also withstand high stress and strain levels without deformation, an attribute essential for high-performance cycling applications.
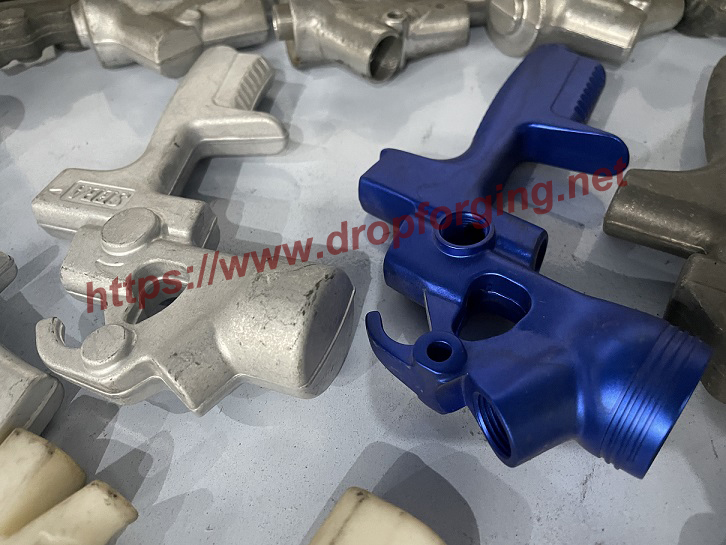
A forged aluminum spray gun body is the central part of a spray gun, which has been formed using a forging process involving aluminum. Essentially, it's the framework that houses various components of the spray gun, including the trigger, nozzle, and paint container.
The term 'forged' signifies the manufacturing process utilized to create the spray gun body. Aluminum forging is a process in which a piece of aluminum is heated and then shaped using a hammer or a press, under high pressure, to achieve a specific design, in this case, the structure of a spray gun body.
The forging process refines the grain structure of the aluminum and aligns it to the shape of the part, thus enhancing its overall strength and durability. Aluminum, and in particular 6061 aluminum alloy, is a popular choice for forging spray gun bodies due to its excellent mechanical properties, good corrosion resistance, and lightweight nature.
The forged aluminum spray gun body thus produced is not only light and easy to handle but also durable and resistant to wear and tear, making it suitable for heavy-duty applications and ensuring a longer lifespan of the spray gun. Furthermore, it maintains its dimensions and shape even under extreme conditions, ensuring the consistent performance of the spray gun.
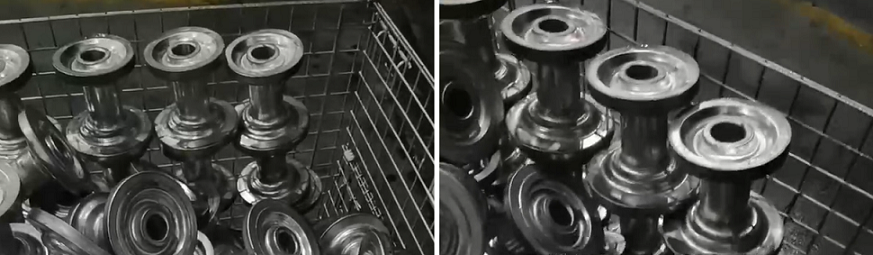
Motorcycles are the epitome of freedom on the open road, but they require specialized parts to keep them running at peak performance. One such component is the wheel hub, which connects the wheel to the axle and provides support for the motorcycle's weight. A forged aluminum motorcycle wheel hub is a popular choice for riders looking for high strength and durability. It is made by taking a solid piece of aluminum and heating it until it becomes malleable. The aluminum is then shaped using a forging press, which applies intense pressure to the material, causing it to take on the desired shape. The result is a high-strength, lightweight wheel hub that is ideal for use in motorcycle applications.
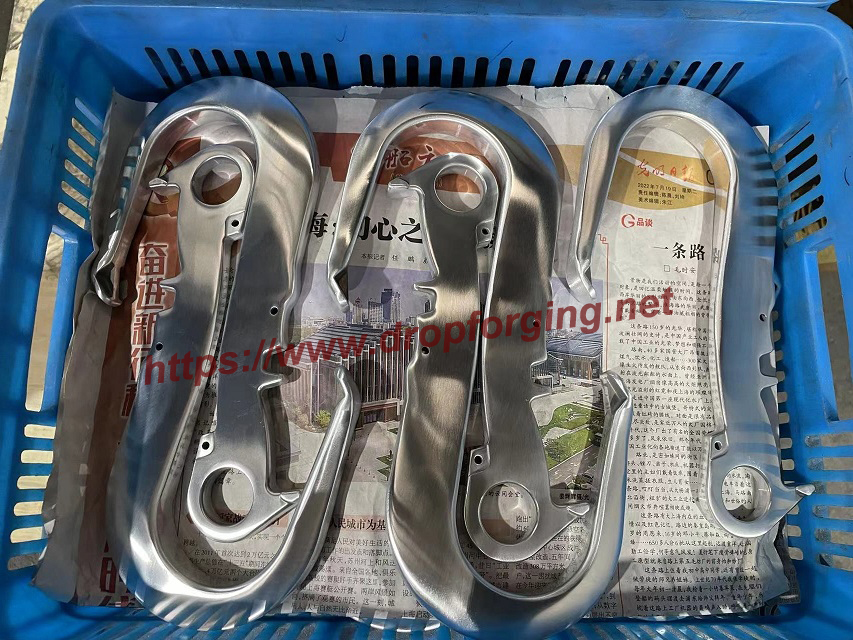
Carabiners are one of the most important safety equipment used in mountaineering, rock climbing, and other outdoor activities. These small, yet robust metal hooks, are often used to secure ropes, harnesses, and other gear, and are crucial in ensuring the safety of climbers and hikers. Aluminum forging is a popular manufacturing process used to produce carabiners due to its many advantages. In this article, we will explore the process of aluminum forging and its benefits for carabiner production.
Forging is a manufacturing process that involves shaping metal by applying pressure to it. Aluminum forging, specifically, is the process of shaping aluminum into various forms, such as carabiners, using compressive forces. In this process, a piece of aluminum is placed between two dies and subjected to high-pressure forces until it takes the shape of the die. The die is a tool that is specially designed to form the metal into a particular shape. The process is often done at high temperatures to make the metal more malleable and easier to shape.
By employing drop forging process, metals (steel, aluminum or copper) can improve its structure and mechanical performance. The drop forgings are deformed by hot processing. Owing to the deformation and recrystallization of the metal, the original coarse dendrites and columnar grains become equiaxed recrystallization with finer grains and uniform size, then the original segregation, looseness, pores and slag inclusions in the ingot are compacted and welded and their structure will become tighter. The plasticity and mechanical performance of the metal are further improved.In general, the mechanical performance of castings is lower than that of forgings with the same raw material. In addition, the forging process can ensure the succession of the metal fibers and keep the forged fibers consistent with the shape of the forged pieces. What’s more, the metal streamlines are intact, which can ensure the parts have outstanding mechanical performance and long working life. With the process of precision die forging, cold kneading and warm kneading, forgings are more superior than castings in performance.
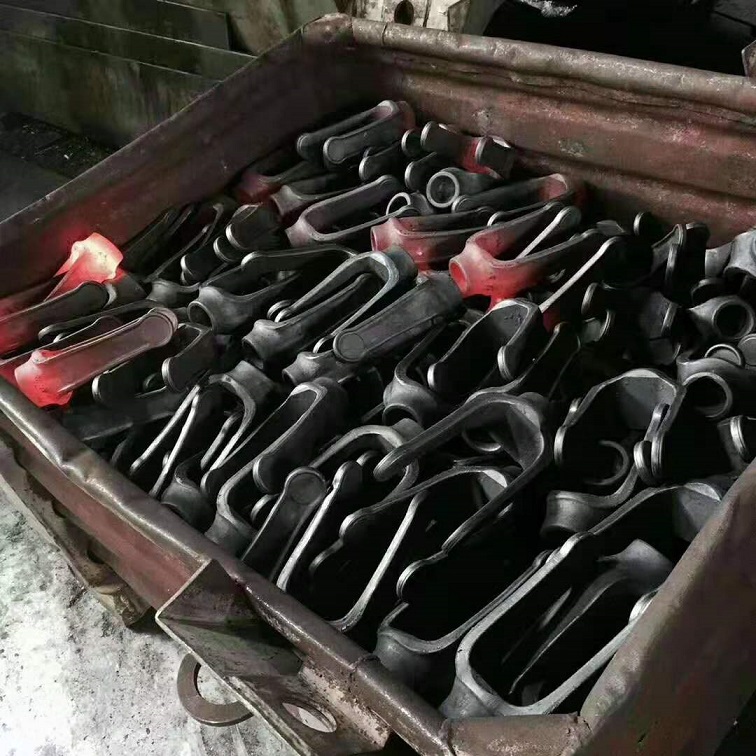
Drop forging of yoke ends is a method of shaping and forming metal using a set of dies (metal-shaping molds). Downward force is applied by the second moving part of the die. This downward force and motion is where the "drop" in drop forging comes from. As the most common metal forging method, it is very suitable to produce yoke ends.
The strength of yoke ends made by drop forging manufacturers can be greatly improved, which is for its particular use by causing the internal grain of the metal to deform to follow the shape of the part. Besides carbon steel, yoke ends can also be drop forged by other metals, such as stainless steel or aluminum. In short, drop forgings are used often to produce hardwares for industries such as aerospace, national defense, automotive, agriculture, construction, hardware, mining, material handling, etc. Many hand tools have “Drop Forged” boldly imprinted on them to indicate their added strength and durability as a result of the forging process. If you have any inquiry on drop forged yoke ends or other drop forged components, pls contact CFS Forge now!
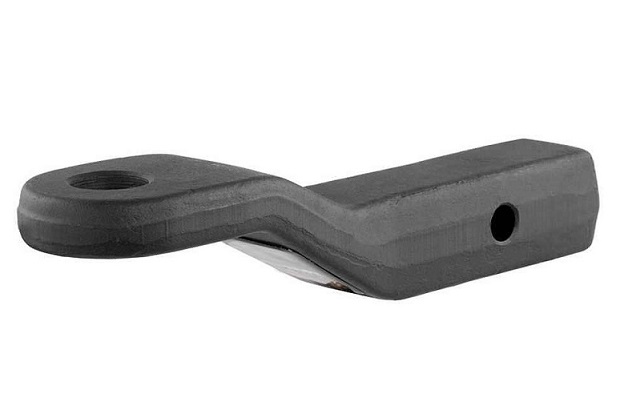
The Drop Forging Process, also referred to as Closed Die Forging, is a process that manipulates hot metal completely within the wall cavity of two dies. The impression for the forging can be in either die or divided between a top and bottom die. The drop forging process can improves the strength of ball mounts by aligning the grain along the lines of potential stress, which cannot be achieved through casting, machining or fabrication. So, drop forging is always used to produce metal components like hitch ball, ball mounts, ect by our customers trailer towing application.Drop Forged Materials selected to produce ball mounts can be either forged steel or forged aluminum. Forged aluminum ball mounts for trailer towing can achieve light weight, but due to the higher material cost, the price of drop forged aluminum ball mounts will be higher than that of drop forged steel ball mounts.As a comprehensive drop forging company, CFS Forge can supply custom service for both steel forgings and aluminum forgings. So, no matter it is forged steel ball mounts or forged aluminum ball mounts, we will be all able to supply in competitive prices.
Hot forging aluminum and aluminum alloys holds many benefits for applications. The process does not impede the ability of manufacturers to manipulate and cut aluminum products easily. Therefore, forged aluminum alloys can be cut into distinctly complex or ornate shapes.When hot forged, aluminum alloys demonstrate some mechanical qualities comparable with steel, and the strength to weight ratio of aluminum exceeds that of steel. In addition, aluminum hot forging can produce a number of surface finishes, ranging from very smooth to relatively sharp.Aluminum hot forgings are generally cost-effective and attractive in their appearance. They allow for high design flexibility and in many cases, the exterior part of hot forged aluminum does not require extensive polishing.For all these reasons, numerous industries make use of aluminum forgings
. The process especially attracts manufacturers seeking to produce large, customized components using aluminum or its alloys.
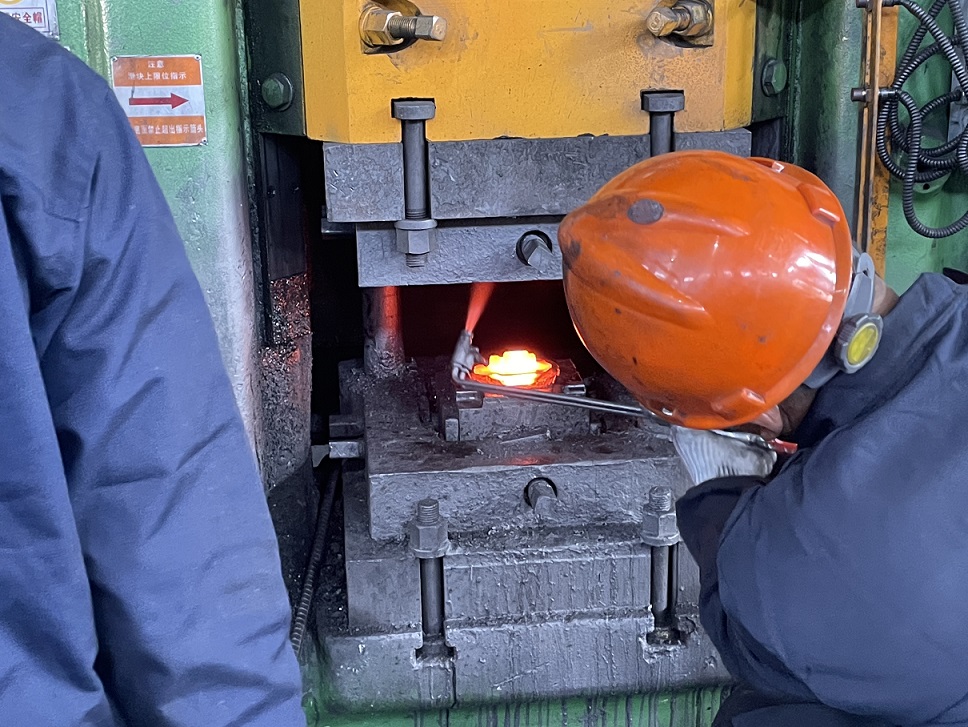
Custom forgings are the forgings made according to the drawings or sample from customers. Here the custom forgings we are talking about are using closed die forging method, not open die forging. Comparing with standard forgings,which have finished mold & dies developing, there is an extra cost for forging dies.
In our company, most drop forged products are all custom forgings excluding some standard high pressure pipe fittings. We are the manufacturer of custom forgings in China and could serve you custom forgings in high strength, close tolerances and low costs. Our forging buying guide will introduce buying procedure in detail.