Drop Forging Heat Treatment
What is heat treatment?
Heat treatment is a hot metal working process referred to material under solid state, by means of heating, heat preservation and cooling, to get the expected organization and properties. So heat treatment is commonly utilized after drop forging process to improve the mechanical properties. So different heat treatment processes have different characteristics, we do heat treatment only follow our customer's requirements. No heat treatment will be done for drop forgings if there is no such demands. The main heat treatment processes include: Normalizing, Annealing, Quenchining, Induction hardening, Case hardening, Solution treatment, etc.
Processes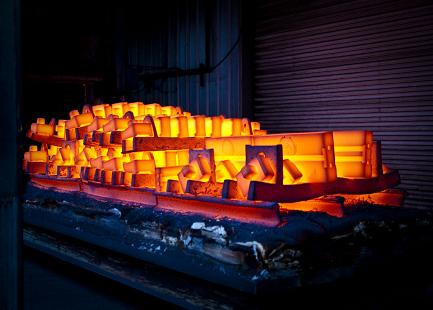
Normalizing
Normalizing is heating steel forgings to temperature above Ac3 or Accm+30℃~50℃, then cooling down slightly faster than annealing after heating preservation. Normalizing nomally worked as advanced heat treatment process for drop forgings. For low & medium carbon steel and low alloy steel drop forgings, we could also use it as the last heat treatment process. We could not use it as final heat treatment process for medium & high alloy steel. Normalizing can help to lower the hardness, improve plasticity, thus to improve subsequent machining property. Besides, it can remove the internal stress produced by machining.
Annealing
Annealing is a heat treatment process that heating drop forgings to above AC3 20~40℃, heating preservation a while, then cooling down with furnace to below 500℃ in the air. Normalizing is a technique used to provide uniformity in grain size and composition throughout an alloy. The term is often used for ferrous alloys that have been austenitized and then cooled in open air.Normalizing not only produces pearlite, but also sometimes martensite, which gives harder and stronger steel, but with less ductility for the same composition than full annealing.
Quenching
Quenching is to heat parts above Ac3 or Ac1, and heat preservation for a while, then fast cooling in water, oil or air. The destination of quenching is to obtain high hardness martensitic structure, thus to improve wear resistance and corrosion resistance. Quenching fits for carbon steel and alloy steel drop forgings with carbon content above 3%. Quenching can completely develop the strength & resistance, produce large internal stress and reduce the plasticity and impact toughness of steel, so quenchining may be required for better comprehensive mechanical property.
Induction hardening
Induction hardening is a surface hardening technique in which the surface of the metal is heated very quickly, using a no-contact method of induction heating. The alloy is then quenched, producing a martensite transformation at the surface while leaving the underlying metal unchanged. This creates a very hard, wear resistant surface of drop forgings while maintaining the proper toughness in the majority of the object. Crankshaft journals are a good example of an induction hardened surface.
Case hardening
Case hardening is a thermochemical diffusion process in which an alloying element,most commonly carbon or nitrogen, diffuses into the surface of a monolithic metal. The resulting interstitial solid solution is harder than the base material, which improves wear resistance without sacrificing toughness.
Solution treatment
Solution treatment is the process that heating drop forgings to single-phase area and constant temperature keeping, thus to get the supersaturated solid solution. Solution treatment is mainly used for stainless steel drop forgings, it will greatly improve further machining property.
Heat treatment is a hot metal working process referred to material under solid state, by means of heating, heat preservation and cooling, to get the expected organization and properties. So heat treatment is commonly utilized after drop forging process to improve the mechanical properties. So different heat treatment processes have different characteristics, we do heat treatment only follow our customer's requirements. No heat treatment will be done for drop forgings if there is no such demands. The main heat treatment processes include: Normalizing, Annealing, Quenchining, Induction hardening, Case hardening, Solution treatment, etc.
Processes
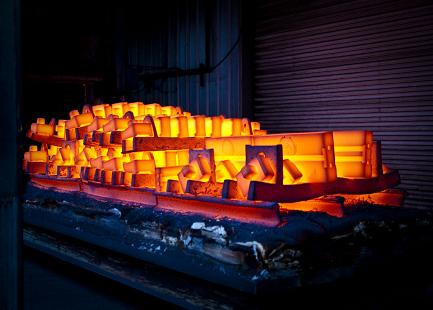
Normalizing
Normalizing is heating steel forgings to temperature above Ac3 or Accm+30℃~50℃, then cooling down slightly faster than annealing after heating preservation. Normalizing nomally worked as advanced heat treatment process for drop forgings. For low & medium carbon steel and low alloy steel drop forgings, we could also use it as the last heat treatment process. We could not use it as final heat treatment process for medium & high alloy steel. Normalizing can help to lower the hardness, improve plasticity, thus to improve subsequent machining property. Besides, it can remove the internal stress produced by machining.
Annealing
Annealing is a heat treatment process that heating drop forgings to above AC3 20~40℃, heating preservation a while, then cooling down with furnace to below 500℃ in the air. Normalizing is a technique used to provide uniformity in grain size and composition throughout an alloy. The term is often used for ferrous alloys that have been austenitized and then cooled in open air.Normalizing not only produces pearlite, but also sometimes martensite, which gives harder and stronger steel, but with less ductility for the same composition than full annealing.
Quenching
Quenching is to heat parts above Ac3 or Ac1, and heat preservation for a while, then fast cooling in water, oil or air. The destination of quenching is to obtain high hardness martensitic structure, thus to improve wear resistance and corrosion resistance. Quenching fits for carbon steel and alloy steel drop forgings with carbon content above 3%. Quenching can completely develop the strength & resistance, produce large internal stress and reduce the plasticity and impact toughness of steel, so quenchining may be required for better comprehensive mechanical property.
Induction hardening
Induction hardening is a surface hardening technique in which the surface of the metal is heated very quickly, using a no-contact method of induction heating. The alloy is then quenched, producing a martensite transformation at the surface while leaving the underlying metal unchanged. This creates a very hard, wear resistant surface of drop forgings while maintaining the proper toughness in the majority of the object. Crankshaft journals are a good example of an induction hardened surface.
Case hardening
Case hardening is a thermochemical diffusion process in which an alloying element,most commonly carbon or nitrogen, diffuses into the surface of a monolithic metal. The resulting interstitial solid solution is harder than the base material, which improves wear resistance without sacrificing toughness.
Solution treatment
Solution treatment is the process that heating drop forgings to single-phase area and constant temperature keeping, thus to get the supersaturated solid solution. Solution treatment is mainly used for stainless steel drop forgings, it will greatly improve further machining property.