Automotive Forgings
The automotive industry is one of the most demanding and competitive sectors in the world, continuously pushing boundaries in technology and design. In order to stay ahead of the curve, manufacturers must embrace innovative processes to produce high-quality, reliable, and cost-effective components. One such process is forging, which plays a critical role in the production of automotive parts. With ISO 9001 & TS 16949 certifications, CFS Forge is uniquely positioned to provide top quality forged components to the global automotive market.
Forging is a manufacturing process in which metal is heated and then shaped by applying localized compressive force. It has been used for centuries to create strong, durable metal parts, and it remains a popular choice for automotive components today. Some of the key advantages of forging in automotive applications include:
Steel and aluminum are the two primary materials used in closed die forging for automotive applications. Each material offers unique advantages in terms of strength, weight, and corrosion resistance.
Steel Forging
Steel has long been a popular choice for automotive components due to its exceptional strength and durability. Forged steel automotive components exhibit improved mechanical properties, such as increased tensile strength and impact toughness, making them ideal for critical applications like engine components, transmission systems, and suspension parts. Moreover, steel forgings provide excellent resistance to wear and fatigue, ensuring long-lasting performance.
Aluminum Forging
Aluminum is a lightweight material that has become increasingly popular in the automotive industry due to its ability to reduce vehicle weight and improve fuel efficiency. Aluminum forgings offer a high strength-to-weight ratio, making them ideal for applications where weight reduction is crucial, such as wheels, steering components, and suspension parts. In addition, aluminum is highly resistant to corrosion, ensuring the longevity of the forged components.
CFS Forge is a premier manufacturer of forged components for the automotive industry, offering both steel and aluminum forging solutions. With a commitment to quality and innovation, CFS Forge has become a trusted partner for automotive manufacturers worldwide.
Key Features of CFS Forge:
Forged parts play a vital role in various automotive applications, contributing to the overall performance and safety of vehicles. Some of the key applications include:
As the automotive industry evolves and embraces new technologies, forging is expected to remain a critical manufacturing process for the production of high-quality components. Some key trends and developments include:
Whether you are in need of steel forging or aluminum forging for your automotive components, CFS Forge is always the right partner for you to look for. Contact us now and send us the inquiry, we will be pleased to offer you our most competitive prices asap!
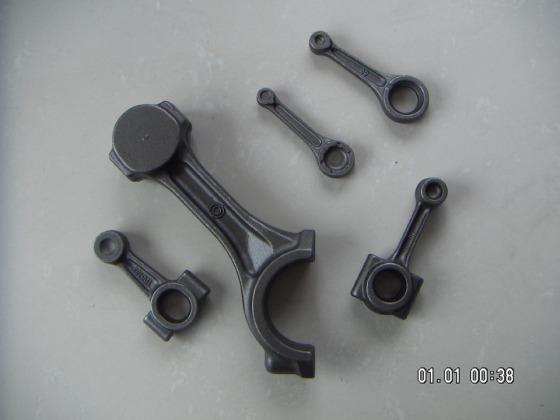
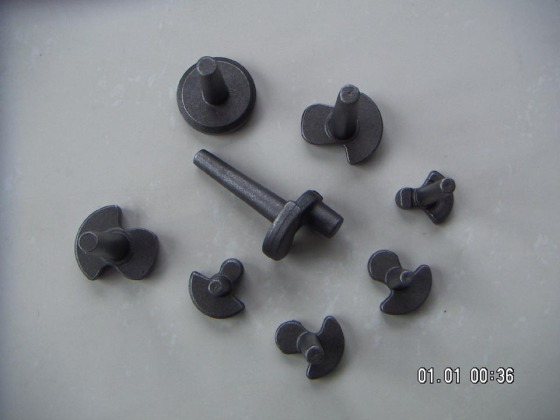
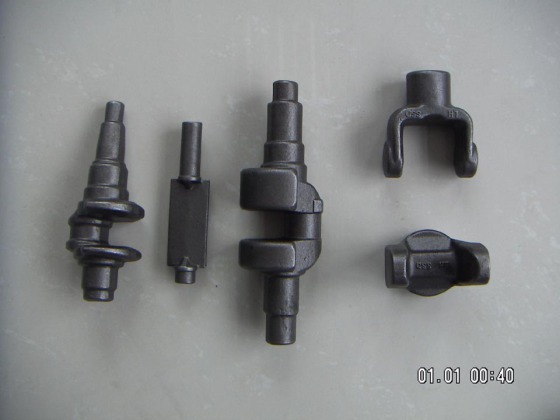
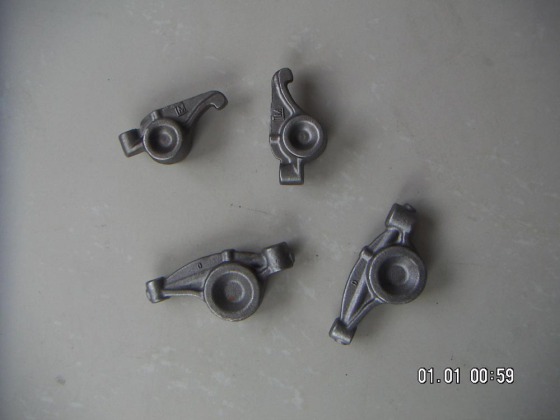
The Role of Forging in the Automotive Industry
Forging is a manufacturing process in which metal is heated and then shaped by applying localized compressive force. It has been used for centuries to create strong, durable metal parts, and it remains a popular choice for automotive components today. Some of the key advantages of forging in automotive applications include:
- Enhanced strength: Forged parts have a more refined grain structure, which increases their strength and fatigue resistance. This is particularly important in the automotive industry, where components are subjected to significant stress and must withstand harsh operating conditions.
- Improved reliability: Forging helps to eliminate internal voids and porosity, which can lead to premature failure. This ensures that forged automotive components have a longer service life and fewer instances of malfunction.
- Cost efficiency: Forged parts typically require less machining and finishing than other manufacturing processes, reducing production time and costs. Additionally, forging can produce complex shapes with minimal waste, resulting in lower material costs.
Common Forging Materials for Automotive Applications
Steel and aluminum are the two primary materials used in closed die forging for automotive applications. Each material offers unique advantages in terms of strength, weight, and corrosion resistance.
Steel Forging
Steel has long been a popular choice for automotive components due to its exceptional strength and durability. Forged steel automotive components exhibit improved mechanical properties, such as increased tensile strength and impact toughness, making them ideal for critical applications like engine components, transmission systems, and suspension parts. Moreover, steel forgings provide excellent resistance to wear and fatigue, ensuring long-lasting performance.
Aluminum Forging
Aluminum is a lightweight material that has become increasingly popular in the automotive industry due to its ability to reduce vehicle weight and improve fuel efficiency. Aluminum forgings offer a high strength-to-weight ratio, making them ideal for applications where weight reduction is crucial, such as wheels, steering components, and suspension parts. In addition, aluminum is highly resistant to corrosion, ensuring the longevity of the forged components.
CFS Forge: A Leading Manufacturer in the Chinese Automotive Forging Industry
CFS Forge is a premier manufacturer of forged components for the automotive industry, offering both steel and aluminum forging solutions. With a commitment to quality and innovation, CFS Forge has become a trusted partner for automotive manufacturers worldwide.
Key Features of CFS Forge:
- ISO 9001 & TS 16949 certified: These certifications demonstrate CFS Forge's commitment to the highest quality standards and best practices in automotive manufacturing.
- Advanced forging equipment: CFS Forge utilizes state-of-the-art forging equipment, including hydraulic presses and hammers, to ensure precision and consistency in its products.
- Expertise in materials: CFS Forge is well-versed in working with a variety of steel and aluminum alloys, ensuring that the most suitable material is used for each application.
- In-house tooling and design: CFS Forge's in-house tooling and design capabilities allow for rapid prototyping and customized solutions, meeting the unique needs of each automotive client.
- Comprehensive quality control: CFS Forge employs rigorous quality control measures, including non-destructive testing and dimensional inspection, to guarantee the reliability of its forged components.
Applications of Forged Components in the Automotive Industry
Forged parts play a vital role in various automotive applications, contributing to the overall performance and safety of vehicles. Some of the key applications include:
- Engine components: Forged parts such as connecting rods, crankshafts, and camshafts are critical to engine performance, with their increased strength and durability ensuring optimal operation.
- Suspension and steering systems: Forged components like control arms, tie rods, and knuckles provide the necessary strength and precision for safe and responsive vehicle handling.
- Transmission systems: Forged gears, shafts, and clutch components offer superior wear resistance and load-bearing capabilities, which are essential for smooth and efficient transmission operation.
- Brake systems: Forged brake calipers and rotors provide improved heat dissipation and increased strength, ensuring reliable and effective braking performance.
- Structural components: Forged parts such as subframes and cross members contribute to the overall structural integrity and safety of a vehicle.
The Future of Forging in the Automotive Industry
As the automotive industry evolves and embraces new technologies, forging is expected to remain a critical manufacturing process for the production of high-quality components. Some key trends and developments include:
- Lightweight materials: As manufacturers strive to reduce vehicle weight and improve fuel efficiency, lightweight materials such as aluminum and high-strength steel will become increasingly important in forging applications.
- Electric vehicles: The growing demand for electric vehicles (EVs) presents new opportunities for forging, with components such as motor shafts, battery housings, and cooling systems requiring strong and lightweight forged parts.
- Advanced manufacturing techniques: Innovations in forging technology, such as isothermal forging and precision closed-die forging, will enable the production of increasingly complex and intricate automotive components.
- Integration with additive manufacturing: The combination of forging and additive manufacturing technologies, such as 3D printing, will enable the creation of hybrid components that offer improved performance and reduced production costs.
Contact Us
Whether you are in need of steel forging or aluminum forging for your automotive components, CFS Forge is always the right partner for you to look for. Contact us now and send us the inquiry, we will be pleased to offer you our most competitive prices asap!
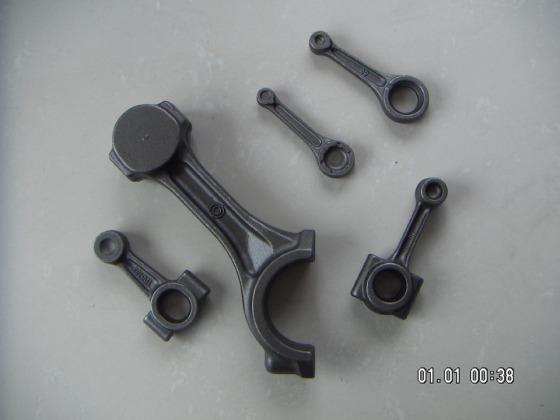
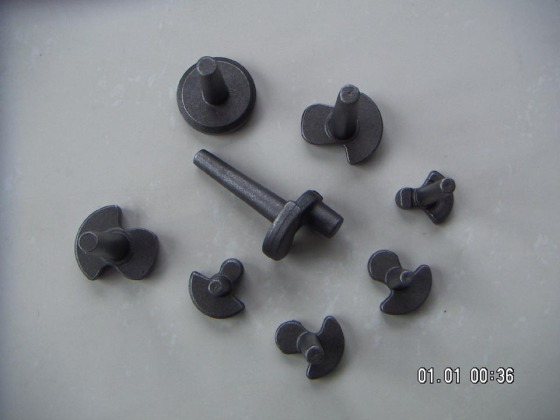
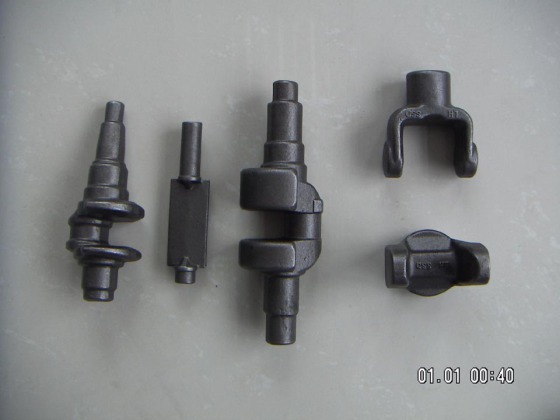
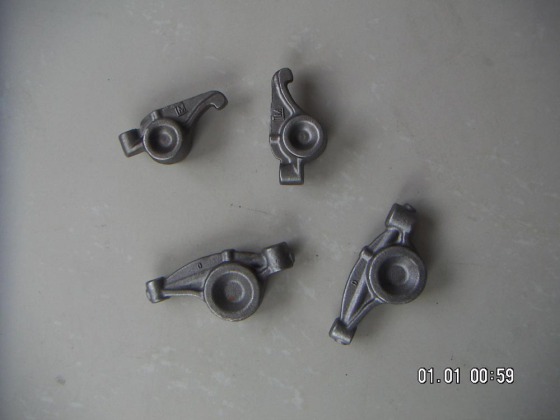