Anodization for Aluminum Forgings
Anodization or Anodizing treatment is the common surface finishing/coating method used for aluminum components, including aluminum castings, aluminum forgings, and even machined aluminum parts. Aluminum forged part is "anodized" for corrosion resistance, improved appearance, hardness & wear resistance, and for a number of specialized reasons like better glue-ability (adhesive bonding) for structural use, improved paint adhesion, and enhanced capacitance in electronic applications. Aluminum forgings are better than castings for anodizing due to a denser, more homogeneous microstructure. CFS Forge is the leading manufacturer for finished aluminum forgings, including closed die forging, cnc machining, surface finishing, heat treatment. So we can also deal with aluminum forgings that require further anodization. Here we introduce anodization for aluminum forgings in detail:
There are normally four stages in the process: pre-treatment, anodising, colouring (where required) and sealing. The most frequent type of anodising is natural anodising. The electrolytic process takes place once the aluminum forging surface has received the appropriate mechanical or chemical pre-treatment and has been thoroughly cleaned.
Preparation before anodization includes processes of removing sharp edges, making smooth roughness, leaving certain machining allowance caused by thickness of the coating layer, designing special jigs, and protecting the not required anodizing surface.
We can general divide anodization methods for aluminum forgings into hard anodization and soft anodization.
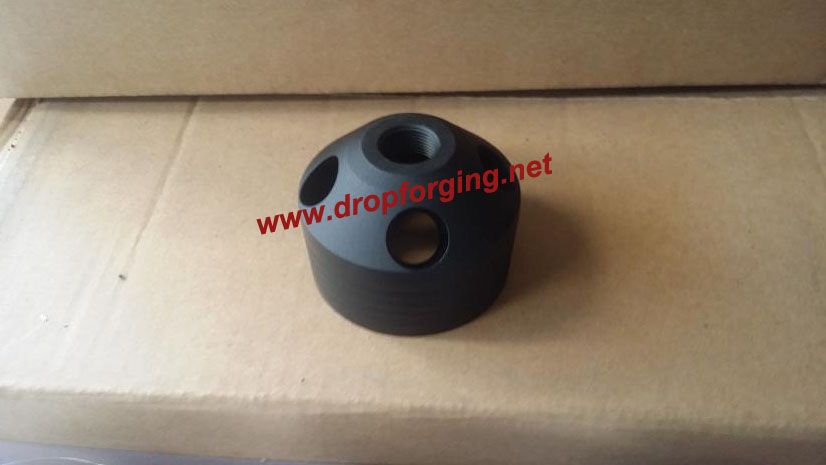
Hard anodizing is a thick film anodic oxidation process, which is a special anodized surface treatment process for aluminum forgings as well as other aluminum components. General thickness of hard anodized film is 40-70 um.
Advantages of Hard Anodizing for Aluminum Forgings:

So, in order to reduce the weight of the product and protect the environment, many metal components are converted into aluminum forging with hard anodizing treatment, which were originally produced in steel forgings with hard chrome plating. More advantages of aluminum forging...
If you have aluminum forgings requiring anodization treatment, please contact us.
Process and Methods
Preparation before anodization includes processes of removing sharp edges, making smooth roughness, leaving certain machining allowance caused by thickness of the coating layer, designing special jigs, and protecting the not required anodizing surface.
We can general divide anodization methods for aluminum forgings into hard anodization and soft anodization.
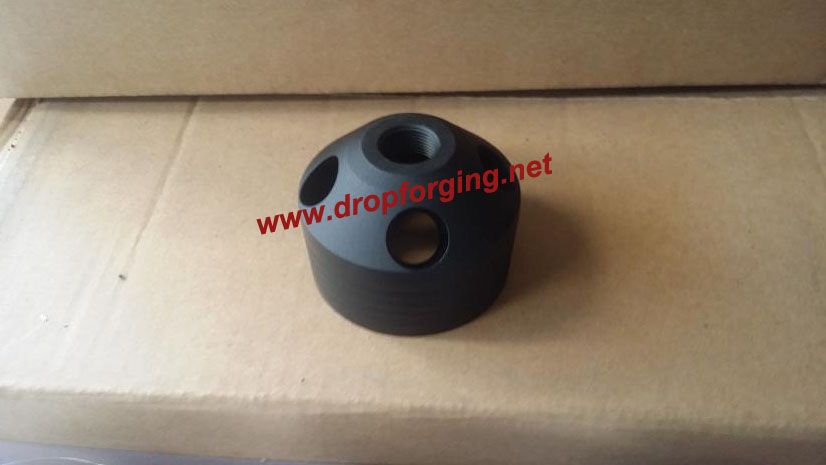
Hard anodizing is a thick film anodic oxidation process, which is a special anodized surface treatment process for aluminum forgings as well as other aluminum components. General thickness of hard anodized film is 40-70 um.
Advantages of Hard Anodizing for Aluminum Forgings:
- The surface hardness of aluminum alloy forgings after hard oxidation can reach up to HV500.
- The oxide film thickness is 25-250um.
- Strong adhesion. according to the oxidation characteristics generated by hard oxidation: 50% of the oxide film penetrates inside the aluminum forgings and 50% is attached to the surface of aluminum forgings (bidirectional growth).
- Good insulation: the breakdown voltage can reach 2000V (perfect seal).
- Good abrasion resistance.
- Non-toxic: Oxidation film and electrochemical process used to produce anodic oxide film should be harmless to human body.

So, in order to reduce the weight of the product and protect the environment, many metal components are converted into aluminum forging with hard anodizing treatment, which were originally produced in steel forgings with hard chrome plating. More advantages of aluminum forging...
If you have aluminum forgings requiring anodization treatment, please contact us.